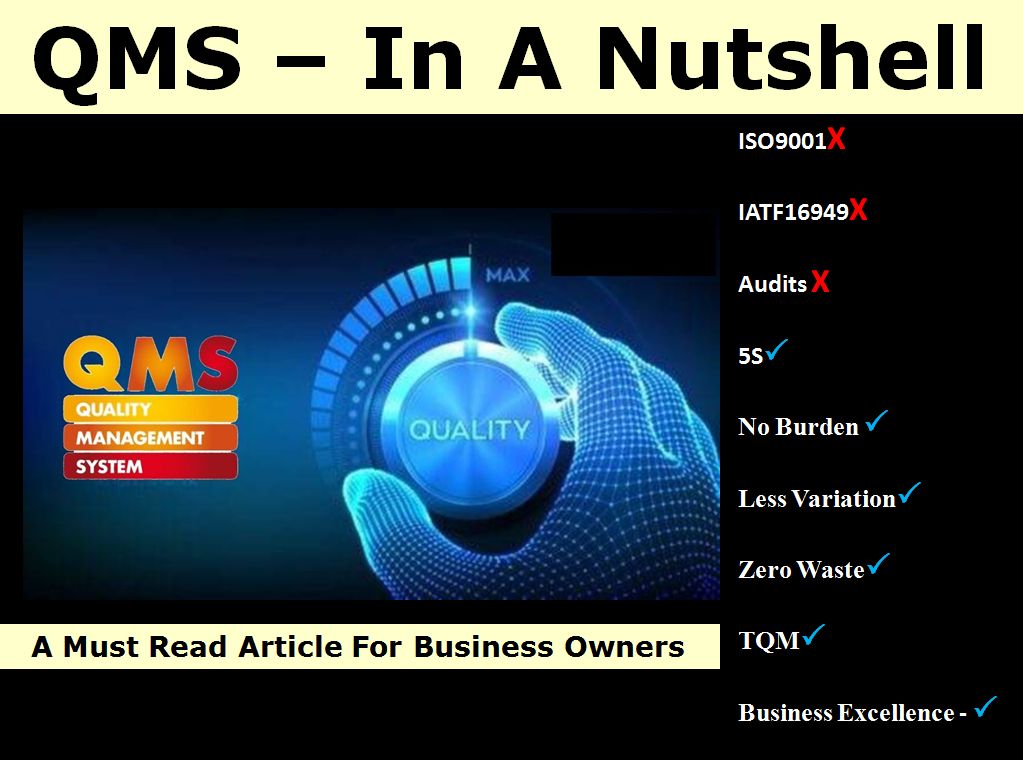
QMS – Quality Management System is a vital
philosophy every company needs to follow. But in the current scenario, the
entire market is made to run after certifications like ISO9001:2015 & IATF16949:2016
which has largely diluted the need for customizing QMS as a philosophy to suit
the companies, their employees & their customers.
Running after certifications have spoiled the
customization & implementation required to build an unquestionable QMS that
satisfies stakeholders (Employees, CEOs, Board of Directors, Share holders,
suppliers, customers & end customers).
Running after certifications & making it mandatory
have built so many blind spots just to satisfy the auditors like doing MSA for
“visual inspectors eye sight” & Cp, Cpk study for tool dominant processes
like sheet metal working, foundry processes etc. In my tenure with Iris Mfg.
& Hinduja, I was able to make auditors understand these & in some cases
I have brought these in written in quality manual itself.
So what has to be done? How to proceed w.r.t building
a self sustaining customized QMS? See the below image & start proceeding
towards this direction which will simplify & help owners to build a self
sustaining customized QMS that will move the companies towards profitable path
forever.

Before explaining how to proceed further using the
above single page nut shell of Muri-Mura-Muda, let me clarify that I don’t
believe in following or copy-pasting Japanese, American & German models.
You can ask, then why I have used the Japanese term Muri-Mura-Muda in the above
nutshell. Such Muri-Mura-Muda (right burden, right variation, no waste)
concepts are nothing new to us, these were taught to us right from Gurukul form
of education. Instead of starting from there, I am starting from these Japanese
terms to make everyone understand how to build a strong QMS in simple ways.
This applies to all other foreign terms I use here & everywhere hereafter.
Prior to drilling deep into building muri-mura-muda,
the first step is to make 5S a habit. 5S is the base upon which the QMS has to
be built. Whatever is built as QMS, without 5S will collapse one fine day all
of a sudden. To explain this point in a simple manner, I would suggest seeing
an advertisement. In this advertisement the pilot student & a pilot
starts their flight & flies in the sky. Then the student notices the pilot
is also a student from the cap he is wearing as both the caps for the student
& the coach are the same, the only difference is the word “coach” &
“student” mentioned on top. Somehow they manage to land the flight safely in
this advertisement. A student asked me, quoting this advertisement that “how
can this incident be avoided?” during a six sigma black belt course in Coimbatore.
Here in such a situation such a confusion could have been easily avoided if 5S
was followed by their institution strictly. How? This error can be simply
avoided by providing different color caps or uniforms to coaches & students
which will differentiate them visually. 5S would have addressed well in advance
would have helped them to avoid such situations.
Now the team must concentrate on building 6M
conditions that respect muri-mura-muda concepts. 6M means 1.Men, 2.Machine,
3.Methods, 4.Materials, 5.Measurement, 6.Mother Nature.
How to build 6M conditions that respect muri-mura-muda
concepts? Here is how it can be done,
1.Men – Competency i.e, qualifications, skills,
experience
2.Machine – Pp, Ppk Studies, TPM
3.Methods – PFD, PFMEA, Control Plan, VSM
4.Materials – Right materials at right cost at right
time
5.Measurement – Calibration & MSA
6.Mother Nature – Right environment (Total Quality
Environment or Preventive 5S)
7.*Money – Loss proof cash flow practices
6M is the general term used which if built rightly
will bring a sustainable, profitable QMS. In my own experience I am adding 7th
M i.e, money to it; because money decides about the kind of 6M owners can
build.
Again all the above hints provided are separate
subjects that need separate articles, anyhow these hints will help you in
building what is required if you already have some basic ideas about these.
7Ms that support each other in providing products
& services with right quality (effectiveness) & right speed
(efficiency) will be enjoyed by customers. A satisfied customer brings you more
income. And this 7th M income will help you to strengthen your remaining 6Ms
strong, stronger & strongest progressively.

Ok. Now you have strong 7Ms & you have made 5S a
habit. Here itself you might be already in profit. To further strengthen your
quality & speed which will result in sustained profits, you can work out on
strengthening Muri-Mura-Muda.
While preparing for Muri-Mura-Muda, it is important to
map your business processes. Any business process starts with reaching
potential customers seeking orders. Keeping this or whatever you do as your 1st
process, keep on asking what next & build a pakka business map. While
drafting your business process map it is advisable to do it in a 5W-2H
methodology, a sample is attached below. 5W-2H means What, Who, When, Why,
Where, How, How many. For every process step it is better to define
·What is to be done?
·Who will do it?
·When it has to be done?
·Why does it has to be done?
·Where it has to be done?
·How it has to be done? If this
needs to be elaborated further, a suitable work instruction can be referred to.
·How many refers to quantity or
frequency for performing the activity repeatedly
Once this is done, the owners will be having a broader
perspective of their business & the entire team involved also will have a
better idea about upstream & downstream business processes to drill deep
further into Muri-Mura-Muda.

Muri (無理)
is a Japanese word meaning "unreasonableness; impossible; beyond one's
power; too difficult; by force; perforce; forcibly; compulsorily;
excessiveness; immoderation", and is a key concept in the Toyota
Production System (TPS). So owners have to see any overburden or unreasonable
practices or demand is there in their entire business process flow.
Now the owner with his team has to review the entire
business process for any overburden or unreasonable practices. Visuals of
Muri-Mura-Muda will give an understanding about what has to be done. In this
case the vehicle is overloaded (machine category of 7M). A simple solution for
the same is also provided in the picture. Here I want to mention a quote
“Business isn’t complicated, we complicate business” which is vital for the
thinking process of the team while approaching for solutions. The same can be
written this way also “Solutions are not complicated, we complicate solutions”.
Keeping this in mind, the owner with his team has to review the entire business
process for overburden problems & standardize the best practice for all the
7M conditions. The razor example mentioned below will help to understand how
“simple solutions” will help.

Once Muri is addressed, the next step is to address
Mura. Mura (斑) is a Japanese word meaning
"unevenness; irregularity; lack of uniformity; non-uniformity;
inequality", and is a key concept in the Toyota
Production System (TPS). Here we must understand the law of nature is
variation & variations will be there inbuilt in everything. A simple
example to make everyone understand this point is, all humans have eyes, nose,
and ears only on their face, but does everyone look alike? That is how nature
operates, every face has the same details, but minor inbuilt variations makes
every face unique & 700 crore faces exist on the earth presently. To
address Mura as usual, the owner with his team has to review the entire
business process to fix variation issues. Apart from business processes, the
team has to review special characteristic (fit, function, performance
requirements or subsequent processing of the product) tolerances & bring
down variations within 50% of the tolerance from the midpoint of the spec. For
example if a tolerance specification is 9.8 to 10.2, the team must maintain it
between 9.9 to 10.1 all the time & adequate 7M conditions must be built to
maintain it at this level. Note this needs to be done for the special
characteristics only & not for the entire characteristic. If a component
has 30 specifications as per drawing, hardly 3 to 5 characteristics will be
marked as special characteristics by the customer or by the internal team. For
bringing down variation through six sigma means, all the training programs will
suggest identifying projects & follow DMAIC cycle. DMAIC means Define,
Measure, Analyze, Improve & Control. But many of the business process
special characteristics (as identified by the owner & the team for their
business processes) & component’s special characteristics variations can be
maintained within 50% of the tolerance zone from mid point by just using simple
problem solving tools or by understanding & adjusting the 7M conditions.
At this juncture I want to mention how we solved a
long existing problem at our client end. Here the problem is OD (Outside
diameter) oversize undersize problem occurring on a sophisticated CNC turning
machining. Around 1% was rejected due to this, where during our initial
discussions the team involved was pointing out to many things including low
salary. I immediately rejected the low salary term quoting “I will give one
lakh salary to the operator for one month at least, can he run the component at
zero rejection levels?” Team said sorry & started drilling deep into the
issue. Actually there is nothing to drill deep into the issue. As a six sigma
rule, for bringing zero error the machine has to be investigated further, I
have gone on this line. Interrogating the operator I came to know such an
oversize undersize problem occurs whenever power goes off & machine has to
be started. For a few components after power off & on, the variation occurs
& becomes normal after. Then I contacted the manufacturer of the machine,
they asked us to send a company person to their factory where they have similar
machines to understand & provide solutions. A maintenance person from the
company visited the machine manufacturer & together after understanding the
issue, the machine manufacturer asked the maintenance person to check if the 5
bolts on the lead screw are fully tightened or not. Coming back to the factory,
the maintenance person found 1 out of 5 lead screws was loose & he
tightened the same. This resulted in bringing the machine back to normal &
rejections have come back to zero. Zero undersize or oversize on OD.
So please remember to bring zero error or six sigma,
manufacturing organizations must investigate their machines & service
organizations must investigate their process sequence & steps. Doing
anything else like blaming men will not provide any results, it will spoil things
further. But here I want to mention men also play a vital role in building or
spoiling systems, hence they have to be attended & motivated carefully.
Because 7Ms are responsible for the product or services offered to the
customers & Men involved controls the other 6Ms. There are men who maintain
their share autos like Benz & there are men who maintain their Benz like
share autos. In this angle men involved play a vital role.
Once Mura is addressed, the next step is to address
Muda. Muda (無駄) is
a Japanese word meaning "futility; uselessness;
wastefulness", and is a key concept in lean
process thinking, like the Toyota Production System (TPS). To address
Muda as usual, the owner with his team has to review the entire business
process to drive out all sorts of wastes. Here priority has to be given to
drive out waste from the production process by revisiting process flow one by
one. Value stream mapping will help to achieve this fully. A separate article
is written on our site for Value Stream Mapping – In A Nutshell. Refer to how
to proceed further to drive out wastes from the production process as well as
business process.
When you do all the above activities meticulously, it
will help all the companies to always be on a profitable path. All the above
activities can be done one by one or in parallel if the team has adequate
understanding about all the activities & the progress can be recorded,
tracked & followed-up till completion. While doing all the above, build a
strong documentation process (task management / activity tracker) which will
help to face Internal 1st party, Customers 2nd party
& certification bodies 3rd party audits. Any audit will start
with verifying the satisfaction level of the customers (internal / external
customers), doing all the above will give 100% internal & external customer
satisfaction. Internal rejection PPM & external rejection PPM will prove
the satisfaction levels on paper are valid. Any audit shall end here itself, as
there is nothing to audit further, but for the sake of auditing, auditors may
extend their audits. At this point, I would suggest all the owners & team
to discuss appropriately with their auditors (1st, 2nd
& 3rd party) to keep the audit days & auditing frequency as
min as possible. Frequent audits will demoralize the team. It is even better to
allow the customers & 3rd party auditors rarely that too on a
need basis if at all any crisis needs their attention. Agreements with
customers & certification bodies need to suitably address this point.
To conclude, let me summarize “QMS – In a Nutshell” in
Swami Vivekanandha style,
· Profit
is potentially divine.
· The
goal is to manifest this Divinity by controlling 7Ms, external and internal.
· Do
this either by 5S or muri, or mura, or muda — by one, or more, or all of these
and be free.
· This
is the whole of QMS. ISO9001, or IATF16949, or lean six sigma, or books, or
training, or documents, are but secondary details.
· So
long as even a single specification in my company is out of control, my whole
team has to correct it and prevent it, anything excluding that is unreligious
QMS.
· Arise,
awake and stop not till the goal is reached.
· Competency
(Education, skills, experience) is the manifestation of perfection already in
man.
· Religious
QMS practice is the manifestation of divinity already in man.
· Serving
customers is serving God.
When all these
things were successfully happening you can confidently say that your company is
a TQM company or you have attained Business Excellence. Even if you don’t say,
your customers will say this.
One final word, do not think all the above can be
followed only by companies. All these can be followed by schools, colleges,
shops, even by small roadside shops to improve their profit. All these can be
followed in personal life also, by individuals by families as 5S (cleanliness),
reduced variation, zero waste, zero errors will help individuals, families
& homes also.
Thanks for spending your valuable time here. Keep in
touch, keep following & keep supporting us.
Thanks
& Regards,
Devarajan NR,
Chairman – JBEGlobal.com Job
Portal & IATFTrainingPortal.com (Since
2013) Past – Delphi TVS | Rane | Brakes India | Iris Mfg. (Shriram Group) |
Hinduja Foundries | IRS (IRQS) | 9362439124 | devarajan.jupiter@gmail.com
Running after certifications have spoiled the customization & implementation required to build an unquestionable QMS that satisfies stakeholders (Employees, CEOs, Board of Directors, Share holders, suppliers, customers & end customers).
Running after certifications & making it mandatory have built so many blind spots just to satisfy the auditors like doing MSA for “visual inspectors eye sight” & Cp, Cpk study for tool dominant processes like sheet metal working, foundry processes etc. In my tenure with Iris Mfg. & Hinduja, I was able to make auditors understand these & in some cases I have brought these in written in quality manual itself.