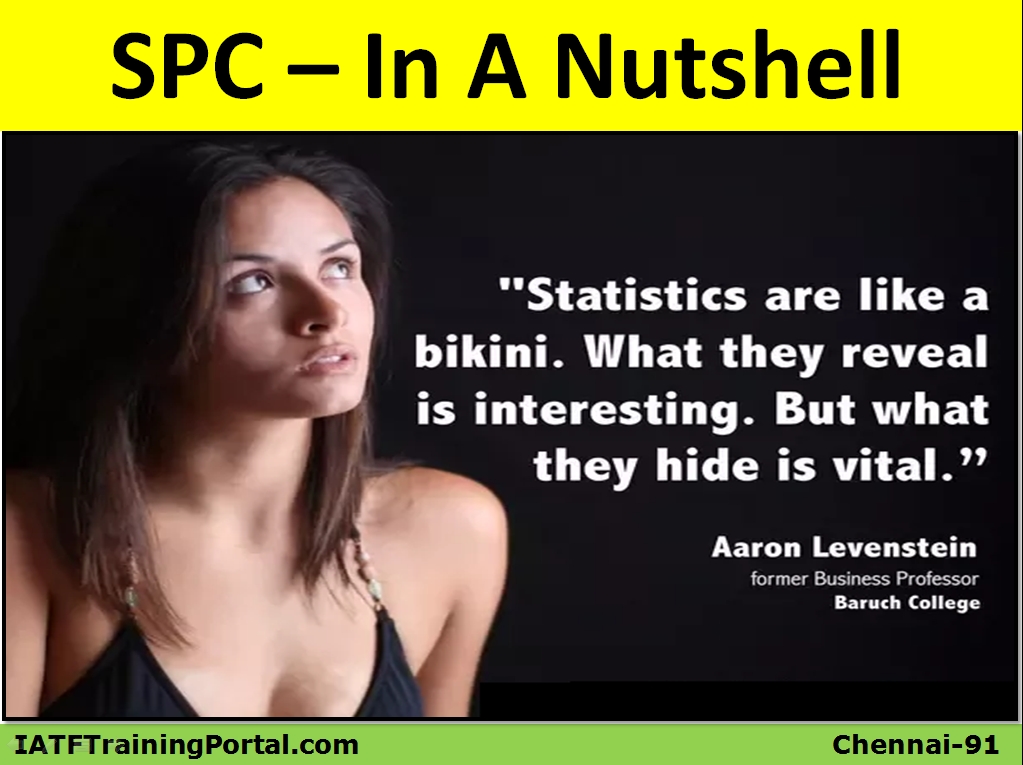
SPC is an ocean,
capturing that in a one page nutshell is not a wise idea. Yet I have tried it
in such a way that everyone atleast understands the conceptual idea of SPC.
This article & seeing some more articles in our page will help everyone to
understand SPC perfectly. I have seen SPC is practiced almost everywhere in a
wrong way or just to satisfy the auditors, not to improve the process or
product.
To emphasize the
importance of SPC, we must know how the Japanese brought a quality revolution.
In 1954, they invited quality gurus like W. Edwards
Deming and Joseph M. Juran to help them improve their businesses. Japan
becoming world no.1 in product quality is the result of the lectures given by
two Americans W. Edwards Deming and Joseph M. Juran. Had Deming and Juran not
given those lectures, Japanese goods would still be of stone-age quality.
These
two quality gurus helped the Japanese to launch their quality revolution. The
senior executives of Japanese companies took personal charge of managing
quality. The companies trained their engineers to use statistical methods (SPC)
for quality control & quality assurance. The companies enlarged their
business plans to include quality goals. Each of these actions was
unprecedented in industrial history. Together, they added up to a massive
change in direction. Japanese companies evolved means of measuring customer
satisfaction, competitive quality and performance that challenged the entire
business community across the world. In contrast, CEOs of world’s leading
companies had long been detached from the quality function. The image below
shows renowned quality gurus & all of them are from USA & Japan. Why no
quality gurus from India? It is because India’s businesses & its CEO’s are
still detached from the crucial quality function, hence the seriousness of
making quality as the no.1 priority is still not happening.
Here
is the list of few things that we are using / used actively, yet will become
obsolete soon or already obsolete, it is due to the quality revolution or the
competitors have built better alternatives for these,
- Shopping malls
- Cash
- Public telephone booths
- Calculators
- Paper maps
- Print catalogues
- Business cards
- Parking meters (pay for parking cars)
- House keys
- Manual-transmission cars
- College textbooks
- Classroom chalkboards
- Post boxes
- In-person voting
- Plastic shopping bags
- Plastic, single-use straws
- Car keys
- Cheques
- Desktop computers
- Cursive writing
- Remote controls
- Fax machines
- Stand alone GPS devices
- Portable music players (iPod)
- Sharing school photos
- Print magazines
- Alarm clocks
- Headphones with cords
- Hotel room keys
- Landline phones (rotary or button telephones)
- Compact Discs CDs
- Paper receipts
- Movies on DVD
- Paper bills
- Paper airplane tickets and boarding passes
- Theatre tickets
- Internet Explorer
- 3G Phones
- BlackBerry Phones
- Encyclopaedias
- Typewriters
- Vinyl Albums
- Film rolls
- Answering Machines
- Slide Projectors
- Overhead Projectors
- Phone Books (Yellow pages)
- The Walkman
- Floppy Disks
- Bench Seats in Cars
- Pagers
- Calculator Watches
- Minidisc
- The Polaroid instant photo
- Video Home System (VHS)
- Dial-Up Modems
SPC helps businesses
attain a profitable quantity & quality. SPC is like a horoscope of a person
where the future can be predicted based on certain inputs in the present or
past. I am 100% sure that most of the owners believe in astrology & vastu, like this if they believe in SPC, they can
escalate their businesses to world class levels. Exactly this is what the
Japanese did, i.e, believing in SPC that made them world no.1 in quality. It is
important to quote about Mr.Aaron Levenstein (1913–86) who was an author and
Professor of Business Administration at Baruch College. In one of his most
memorable quotations he suggested that: Statistics are like a bikini. What they
reveal is suggestive, but what they conceal is vital. Basically, he is saying
that statistics can be used to confuse and mislead the reader. You can
understand these when paid media or fringe groups post a poor picture about
India & its economy by using irrelevant statistics. Hence it is advised to
be careful while interpreting statistics. Do it the right way, if not, you will
be trapped.
SPC
depends on the process i.e, the manufacturing process (7m conditions). It does
not depend on the specification or tolerance given by customers. A company that
builds their manufacturing process to produce the products within 50% of the
tolerance zone (w.r.t special characteristics) from midpoint makes profits
straight away. Others suffer a lot. When NPD team (New Product Development)
builds their product wisely like this, they are complying with all the four
conditions mentioned in the “SPC-In A Nutshell” image straight away i.e, right
first time (RFT) concept. For others, SPC will be like a roller coaster ride
going through all the four phases as mentioned in the “SPC-In A Nuthsell”
image.
“Out Of Control” situation
due to Special Cause Variation
Instead of
a factory example, I will take a hospital example to make you understand the
four phases of SPC. The first phase is “Out of control”. You are visiting a
hospital for a consultation after fixing an appointment over the phone. You
have reached on time & expecting the waiting time for consulting will be
less than one hour. Surprisingly on that day you are made to wait for more than
5 hours, being a specialist doctor who gives consulting only two days a week as
well as you have undergone a major surgery there, you have no option other than
waiting patiently. Being a six sigma person, you can clearly understand on that
specific day some kind of “special cause” is disturbing the entire system of
“doctor consulting his patients”. When I went through such a situation in a
very famous hospital in Chennai, I started enquiring with the team involved in
this process to understand what that special cause was. As it is a well built
hospital with the entire needed infrastructure with adequate manpower,
definitely the reason or cause for delay cannot be a “common cause”. Finally
this delay or variation is due to a special cause, i.e, leave taken by that
specialist doctor last week. Due to this all the previous week’s appointments
were postponed to the next week, increasing the inflow of patients on that
specific day. Expecting this increase they have made some arrangements like two
consulting rooms with his assistants reading the status of the patients &
doctor shuffling between two rooms & giving his decisions quickly based on
the inputs from his assistants. Yet it was insufficient & the customer (the
patient) can easily understand the “Out of control” situation. This is such a
bitter experience which will remain in the memory of the patient, his attenders
& his family for a lifetime.
Situation (or process) “In
Control” as Special Cause Variations are identified & eliminated.
Causes
(remember cause & effect or fishbone diagram?) are responsible for
variation. A process is said to be “In control” when it has no special causes
in it. Special causes are unanticipated, emergent, unpredictable, surprise,
unexpected, non-quantifiable, and unusual. For the waiting time quoted in the
“doctor consulting his patients” example, to bring it into SPC, the team
involved in that process can build a chart by plotting “waiting time” of all
patients. In our example case, the cause or reason is simple & visible; it
may not be the same in all cases. Hence the team may be using control charts,
cause analysis, capability studies to drive out or eliminate the special cause.
Nelson’s 7 rules will help the team in understanding the presence of special
causes, read our article on this title to know more about it.
Situation (or process) “In
Control but not capable”
A process
is said to be “In control” or “Stable” when all special causes are fully
eliminated. A stable, in control process will have variations caused by “Common
causes” only. Variations due to common causes will be due to the inbuilt /
inherent variations present in the 6M Men, Machine, Material, Methods,
Measurement, and Mother Nature. If the NPD team didn’t select the right
combination of 6M conditions during the product / process development, the
common cause variation will be more than the customer specification. So the
situation or the process may be under control, but it may not be “Capable” as
it doesn’t satisfy the customer requirements. Let us go back to our “doctor
consulting his patients” example, there what is the customer requirement? You
have reached the hospital on time & expecting the waiting time for
consulting will be less than one hour. Hence the customer requirement is less
than one hour. In our experience on that one specific day, the waiting time
exceeded more than 5 hours. A special cause is a reason, which the hospital may
avoid in future. I have visited the same hospital for consulting the same
doctor 5 times & the waiting time is 1.5hrs, 1hr, 0.5hrs, 1hr & 5hrs.
Out of these 5 incidents of waiting time, 3 times customer requirement was
satisfied & twice it was not. Out of 5 incidents, once it was due to
special cause, rest 4 incidents the variation that is range (max-min i.e, 1.5 –
0.5 = 1hr) 1hr is caused due to the “common cause” variation. Common cause
variations are natural, predictable, random, constant, regular, inherent,
inbuilt & measureable. To bring down this common cause variation that is
1hr of variation, some changes need to be made in the 6M conditions, mainly on
the machines & processes. Apart from this, just think, how many hospitals
or clinics you visit, ask you about what is your requirement w.r.t waiting time
or how happy are you about their services? Aren’t we lagging in a huge way in
building a quality culture?
Situation (or process) “In
Control and capable”
This is
the preferred situation. Special causes are eliminated & common cause
variation operates within the 50% tolerance zone from midpoint of the customer
requirements. Why 50% of the tolerance from midpoint? The midpoint is expected
to shift or oscillate on both the sides due to no standard practices (sop),
wear & tear, computer response time, poor working conditions, incompetent
persons. Hence if the process is established to operate within 50% from
midpoint, it will automatically take care of oscillations. Hence customer
requirements will be always met & their expectations will be always
fulfilled. In our “doctor consulting his patients” example, the patient’s
waiting time will always be less than 1 hour. When the process is “In control
and capable”, the team must monitor it meticulously through control charts to ensure
the common causes always stay within limits & no special cause signals are
noticed. To monitor this team must select the right control charts relevant to
their operations, reading our article on “Popular control charts – In A
Nutshell” will help you to understand how 8 types of control charts can be used
extensively for all kinds of situations.
Thanks for spending your valuable
time here. Keep in touch, keep following & keep supporting us.
Thanks & Regards,
Devarajan NR,
Chairman – JBEGlobal.com Job
Portal & IATFTrainingPortal.com (Since 2013) Past – Delphi TVS
| Rane | Brakes India | Iris Mfg. (Shriram Group) | Hinduja Foundries | IRS
(IRQS) | 9362439124 | devarajan.jupiter@gmail.com