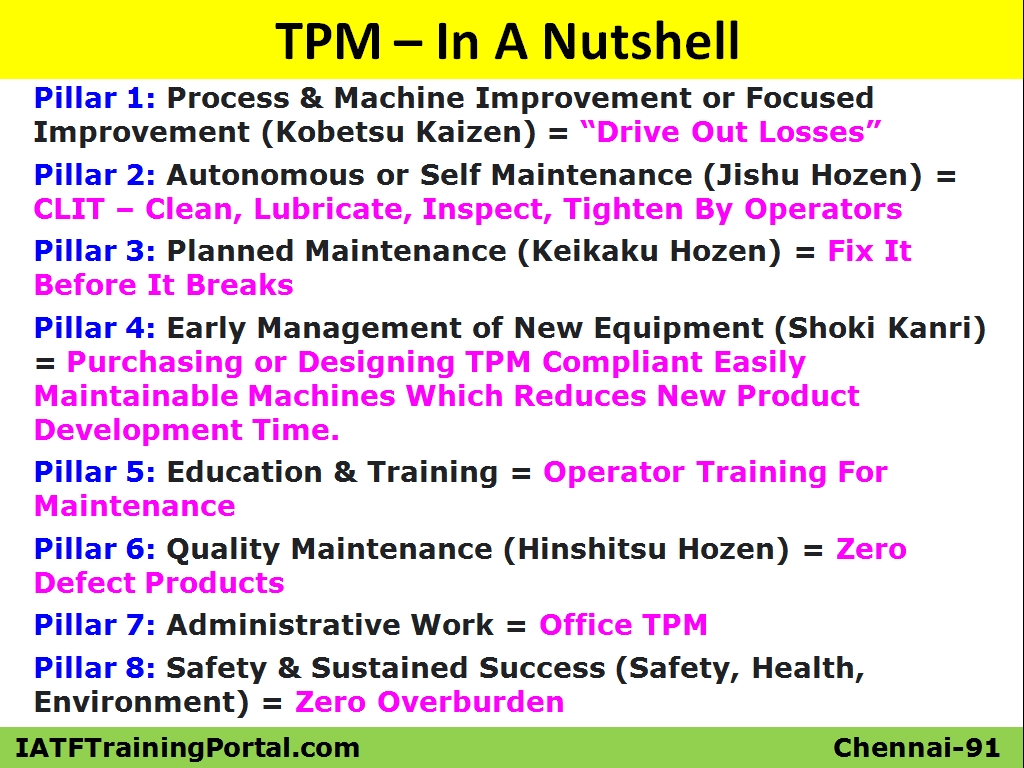
Objectives or Aims Of TPM
1)Zero breakdowns
2)Zero small stops
3)Zero slow running
4)Zero defects and
5)Zero accidents.
Eight (8) Pillars Of TPM
Pillar 1: Process & Machine Improvement or
Focused Improvement (Kobetsu Kaizen) - “Drive Out Losses”
Pillar 2: Autonomous or Self Maintenance
(Jishu Hozen) – CLIT – Clean, Lubricate, Inspect, Tighten By Operators
Pillar 3: Planned Maintenance (Keikaku Hozen)
– Fix It Before It Breaks
Pillar 4: Early Management of New Equipment
(Shoki Kanri) - Purchasing or Designing TPM Compliant Easily Maintainable
Machines Which Reduces New Product Development Time.
Pillar 5: Education & Training (Operator
Training For Maintenance)
Pillar 6: Quality Maintenance (Hinshitsu
Hozen) - Zero Defect Products
Pillar 7: Administrative Work (Office TPM)
Pillar 8: Safety & Sustained Success
(Safety, Health, Environment)
TPM’s performance can be evaluated using the
calculation of OEE i.e, Overall Equipment Effectiveness. OEE percentage tells
how the TPM is performing for the entire factory. OEE = Availability x
Performance x Quality (APQ). Availability is the available time of machines i.e
actual run time (minus stoppages) vs available time. Performance is the actual
output vs expected output (as per set cycle time standards). Quality is the
Actual accepted output (minus rejections) vs total output.
Maintenance of your own motorcycle or bike will
help everyone to understand the TPM in a much better way. So each &
everyone of us knows TPM & we are already practicing it to some extent or
full extent in our daily life with the equipment we are using at our home.
Japanese have split this into a set of activities & grouped it & termed
it TPM for the purpose of betterment of factories, but this TPM culture is
inbuilt in our life & culture, which we did not formulate as a system like
Japanese did.
Pillar-1 – Focused Improvement
(Kobetsu Kaizen) - Drive Out Losses
Kobetsu Kaizen is a Japanese (個別改善)
term which means 'targeted improvement' or 'Focused Improvement'. Focused
improvement (Kobetsu Kaizen) is intended to prevent the accelerated
deterioration of equipment parts. In simple terms Kobetsu Kaizen = “Drive Out
Losses” from machines.
Note: I will explain pillar-1 alone in detail using
a bike (motorcycle) example. Rest of the pillars, i will explain quickly as a
summary instead of going in-depth, it is upto to the reader to expand the idea
mentioned in the pillar-1 example to understand other pillars better. To
simplify things, our body itself is a machine, those who maintain it to TPM
levels stay healthy, happy & live longer, others suffer & living itself
becomes a burden when their body is not co-operating irrespective of their
financial status & social status.
Steps for Kobetsu Kaizen are as follows,
1)Select a model machine or a model line
2)Form team
3)Assess present situation w.r.t to losses in the
selected model machine or model line
4)Drive out losses one by one
5)Standardize & horizontal deployment
1)Select a model machine or a model line:
Let us assume that you have decided to do TPM in your home. You have many
equipment (machines) or spaces (like lines in factories) at your home & you
have to choose one machine or line where you will start your TPM activities.
List various equipments in your home washing machine, AC, Fridge, vacuum
cleaner, car, bike, mixie, grinder, chimney, fans, air cooler, hall, room,
toilets, bathrooms, balcony, kitchen & prioritize which equipment or line
(spaces like hall, room) you will choose for starting TPM. Here we have chosen
a bike as our machine as it has a high risk costing our life.
3)Assess present situation w.r.t to losses in the selected model machine or model line: Here we can assess our bike w.r.to losses on safe riding as well as improving mileage. Image shown below can be used to assess losses.
Breakdown loss is your bike
stopping suddenly during a drive, if you have faced any such situation before;
use that to avoid the same in future. Otherwise in general having a tool box,
air pump, tyre air pressure gauge, spark plug spare, spare tyre & tube will
help you to repair on your own when such sudden breakdown occurs & no
mechanic shop is spotted nearby. Apart from this in my own personal experience,
my new bike broke down twice in the first year of use itself & the reason
is the alternator. In my case, if I have a spare alternator ready & i know
how to replace the alternator, i can travel without any worry.
Set-up & adjustment
is done in the carburettor in idling condition to improve mileage, we must know
this & adjust on our own when we find our bike is switching off suddenly in
idling or during gear shift or at slow speeds.
Idling & minor stoppages
are stopping bike wantedly to avoid any malfunctioning like when you stop your
bike when you feel it is overheated. Here we must check whether we are using
the right cooling solutions (engine oil, gear oil) & the solutions are
working properly to avoid such stoppages.
Reduced speed situations where
you ride at lesser speed. Reasons for this may be worn out tyre, less air
pressure, overheating, overload, and bad roads. If you avoid these reasons, you
can ride your bike at optimum speed to improve mileage & life of your bike.
Defects & rework – inspecting
the bike regularly for defects like small cuts on tyres (which if not attended
will lead to bursting), small stones sticking on tyres, scratches, dents (on
fuel tank may be dangerous) must be done regularly. Keeping our driving
conditions (like driving on good roads) healthy will help us to avoid defects
& rework to maximum extent to improve speed (mileage) & quality (life
of bike).
Yield losses – a motorcycle or
bike has hundreds of parts, each one having a lifetime or expiry time. If any
part fails prior to its lifetime or expiry, it is a yield loss to the owner.
The main yield loss is mileage which can be monitored regularly &
corrected. Apart from this other parts like spark plug, carburettor, tubes,
tyres, seat covers etc., that are changed during the life cycle of the bike
have to be monitored to minimize yield loss.
4)Drive out losses one by one:
Driving out above six major losses will help to improve the speed or output
(efficiency) & quality or life (effectiveness) which will result in
improved OEE%. Some activities planned to drive out losses in our “Kobetsu
Kaizen For Bike” example are having a tool box, air pump, tyre air pressure
gauge, spark plug spare, spare tyre & tube, spare alternator, idling adjustment,
regular inspection, monitoring yield & mileage. Like this for factories,
the machine or line selected must be addressed & analyzed thoroughly to
drive out losses to improve OEE.
5)Standardize & horizontal deployment:
Standardization is documenting all the improvements in respective process flow,
fmea, control plan, work instructions, kaizen sheets, operator training,
checklists etc. This is important to ensure things do not go back to its old
status when manpower or team changes. Horizontal deployment is looking for
opportunities to implement the improvement activities done in this machine
(bike in our case) or line can be done for other machines or lines.
Pillar 2: Autonomous or Self
Maintenance (Jishu Hozen) – CLIT – Clean, Lubricate, Inspect, Tighten By
Operators
Jishu Hozen, which means autonomous or
self-maintenance means “Workplace Ownership: “I operate the machine; I will
maintain it also.”” Through autonomous maintenance initiatives, production
operators are expected to perform the TPM Activities of Cleaning, Lubrication,
Inspection & Tightening on a Daily basis.
Imagine that you are travelling in a bus & it
suddenly gets punctured. What will happen if it is a government bus? & what
will happen if it is a private bus? Private bus driver, conductor & helper
will jump into action & will replace new spare tyre within 10 minutes. They
will ensure this 10 minute did not affect the travel time & ensure
passengers reach the destination on time. If it is a government bus, the conductor
along with passengers will get down & stand as a crowd to stop the upcoming
buses & passengers will get into the buses. This initiative itself will
take 30 minutes to 1 hour. Driver & conductor will report about the
puncture to the maintenance team & will wait till a maintenance truck
arrives with the maintenance team. A bus, driver, conductor, maintenance truck,
maintenance team will waste at least half a day during this recovery action.
The private bus companies have already put forth TPM practice i.e, self maintenance
(Jishu Hozen) in practice, hence the driver, conductor, helper, passenger &
bus owner have built an effective & efficient transport system that
benefits everyone involved. Exactly this is the intention & expectation of
Jishu Hozen w.r.t operators of a machine.
Seven steps for Jishu Hozen are as follows,
1) Clean and Inspect
2) Eliminate Problem Sources & Inaccessible Areas
3) Draw Up Cleaning & Lubricating Standards
4) Conduct General Inspections
5) Conduct Autonomous Inspections
6) Standardize through Visual Workplace Management
7) Implement Autonomous Equipment Management
Pillar 3: Planned Maintenance
(Keikaku Hozen) - Fix It Before It Breaks
The idea is instead of fixing issues after the
breakdown, you do maintenance so it doesn’t breakdown at all. Another very
useful tool is planned maintenance. In Japanese this would be Keikaku
Hozen (計画 保全
for plan; project; schedule; scheme; program; and preservation;
integrity; conservation; maintenance). Sometimes it is also called preventive maintenance or,
if it includes lots of data gathering, predictive maintenance.
Utilize all these six different types of
maintenance strategies to bring machine maintenance to “Fix it before it
breaks” level,
1)Preventive maintenance – includes regular and periodic
(time-based) schedules.
2)Corrective maintenance – occurs when an
issue is noticed.
3)Predetermined maintenance – follows a
factory schedule.
4)Condition-based maintenance – occurs when a
situation or condition indicates maintenance is needed.
5)Predictive maintenance – is data-driven and
impacted by preset parameters.
6)Reactive maintenance – occurs when a total
breakdown or failure appears.
Pillar 4: Early Management of New
Equipment – Purchasing or Designing TPM Compliant Easily Maintainable Machines
Which Reduces New Product Development Time.
The pillar uses the experience and learning
gathered from previous maintenance improvement activities and uses them during
the new machine (design or) purchase and installation and helps in making sure
that the new machinery reaches its peak performance much early than usual.
Following aspects are considered well in advance
during initial purchasing decisions of a machine, which helps in maintaining
the machine later,
- Ease of
cleaning, lubrication and inspection
- Accessibility
of the parts of the machine/ equipment
- Ease of
operation of the machine from the ergonomic aspects of the machine
- Ease of
changeover - clamping, de-clamping, quick adjustments and easy setting
change etc.
- Ease of
understanding and reacting to the feedback mechanisms, visual or sound
indicators.
- Adequacy
of safety features such as light curtains, auto stoppage mechanisms
and safety sensor systems.
Pillar 5: Education & Training
(Operator Training For Maintenance)
Machine operators need to be trained for soft
skills and technical skills. Often factories suffer heavily as the operators
are totally disengaged from the 7M conditions i.e, men, machine, material,
methods, measurement, mother-nature & money. Education & Training helps
operators to fully engage in improving 7M conditions with the primary focus on
Machine & Men (teaming-up).
Pillar 6: Quality Maintenance
(Hinshitsu Hozen) – Zero Defect Products
Quality Maintenance reduces the cost of quality,
rework, repairs, customer complaints and the need for inspection. Problem
solving techniques will help to attain this level. Read our other articles on
SPC, Quality cost, SIPOC for all processes, VSM, QMS – In A Nutshell, PPAP,
Core Tools – In A Nutshell, MSA, FMEA, APQP, 164 Must Read Glossary For Six
Sigma, PPAP, IATF16949 which will help to achieve “Zero Defect”.
Pillar 7: Administrative Work (Office
TPM)
Office TPM concentrates on all areas that provide
administrative and support functions in the organisation. The pillar applies
the key TPM principles in eliminating waste and losses from these departments.
The pillar ensures that all processes support the optimisation of manufacturing
processes and that they are completed at optimal cost.
Pillar 8: Safety & Sustained Success
(Safety, Health, Environment)
Safety, Health and Environment (SHE) is the final
TPM pillar and implements a methodology to drive towards the achievement of
zero accidents. It is important to note that this is not just safety related
but covers zero accidents, zero overburden (physical and mental stress and
strain on employees) and zero pollution. Read our article “QMS – In A Nutshell” which helps
to understand TPM, Lean, Six Sigma, TQM & Business Excellence.
Thanks for spending your valuable time here. Keep
in touch, keep following & keep supporting us.
Thanks & Regards,
Devarajan NR,
Chairman – JBEGlobal.com Job Portal & IATFTrainingPortal.com (Since 2013) Past – Delphi TVS | Rane | Brakes India |
Iris Mfg. (Shriram Group) | Hinduja Foundries | IRS (IRQS) | 9362439124 | devarajan.jupiter@gmail.com