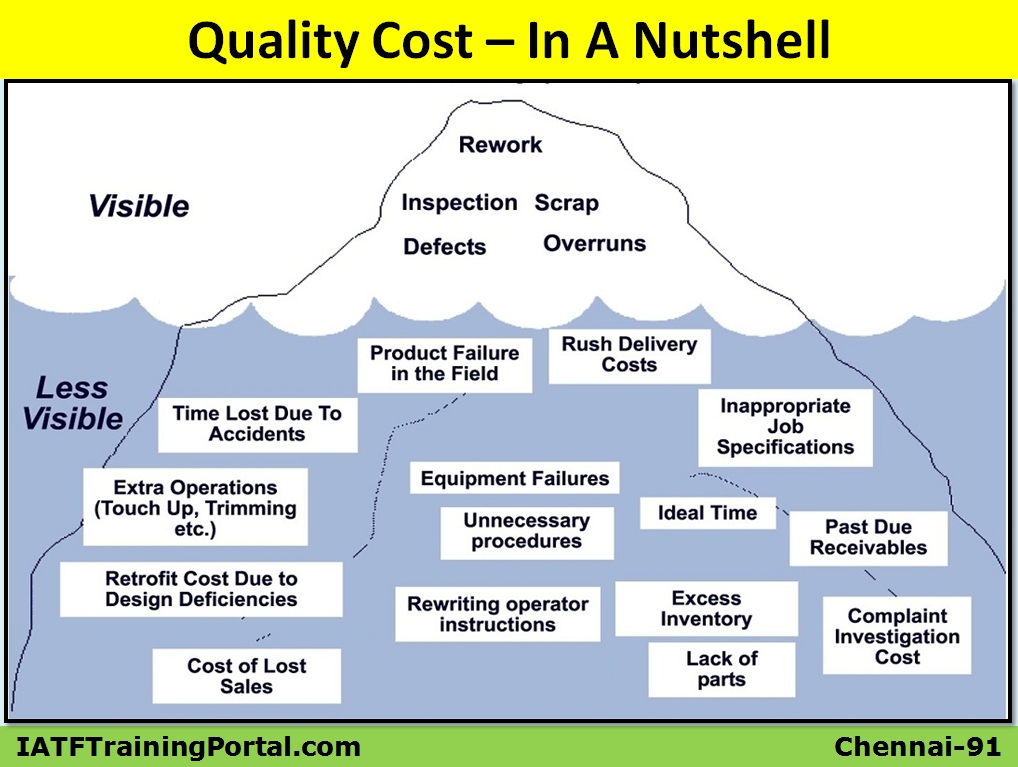
Most of us
confuse the terms QA & QC. It is better to get clarified about this QA
& QC which helps to understand Quality Cost (or Cost Of Quality) perfectly.
Image shown below will help to understand QA & QC better. QA means
prevention i.e, the defect has never happened even once, we have prevented the
defect happening even once completely. Now you can understand prevention (or
QA) is possible during new product development (product / process design) only.
During new product development, the team can work-out strategies which will
help to prevent defects that happened in the past in the similar product or
manufacturing process. QC means detection i.e, all other activities like
incoming, inprocess, final inspection & associated activities.
Hope all of you have already read & understood the “VSM – In A Nutshell” (Value stream mapping) article published by me. Asper VSM, QC is a NVA (Non-value added activity). If you see the costing sheet of a product, you can understand no customer is paying a single penny for QC activities, they only pay for the product produced i.e, for the conversion activities from Raw material to finished goods. Hence it is very important for the owners to completely come out of QC activities or wherever possible outsource these activities. QC is a NVA, still companies are doing it & customers are also demanding it mercilessly. Why? See the below image.It is because of huge money & reputation involved if some defect goes to the end customer. It will totally spoil the reputation & the company may be even forced to shut down its business.
At this point, I request all of you to see this video which will help in understanding why the “cost of quality” is important.
Ford is one
of the reputed Top-3 giants in the USA automobile history. Even Ford faced such
a situation due to poor quality of their car called “Pinto”. Pinto affair
(1971-1980) brought a big setback to Ford money-wise & reputation-wise.
Government & people of the USA wanted the Ford factories to be shut down
immediately due to Pinto cars bursting into flames killing 27 people. Ford
somehow managed to come-out of that issue using their strong legal experts
& somehow survived. Ford brought FMEA from “US Army – NASA” to “Automobile
industry” after the “Pinto affair”. This strengthened the QA aspect of new
product development of Ford & no such similar incident is reported after
that, i.e, Ford has prevented this issue in their future products.
Let us get
into “Cost of Quality” (COQ). The four broader categories of COQ are,
1)Prevention
cost
2)Appraisal
cost
3)Internal
failure cost
4)External
failure cost
Out of the
above four costs, the first two (1)Prevention & (2)Appraisal are “Cost Of
Good Quality (COGQ)”. The last two
(3)Internal Failure & (4)External Failure are “Cost of Poor Quality (COPQ)”.
In this the appraisal cost may be a little bit tricky as all the appraisal cost
cannot be considered as COGQ, some of it have to be considered as COPQ. Team
will have a better clarity about this while doing this practically.
To monitor,
measure, analyze & improve “Quality cost”, the best way is to monitor all the
4 types of costs department wise. Every month all the departments must submit
their quality cost details & the same is to be compiled to derive the
“Quality cost” for the company.
Once all
the four types of costs are collected, it has to be compiled & compared
against the sales. This quality cost details need to be shared to the “Top
Management” on a monthly basis. Cost of quality, its four major categories
& their trends are reviewed by Top Management & any recovery actions
required is discussed & decided & followed-up till completion.
Cost of
poor quality & their trends are also reviewed separately by Top Management
& any recovery actions required is discussed & decided &
followed-up till completion.
Thanks for spending your valuable time here. Keep
in touch, keep following & keep supporting us.
Thanks & Regards,
Devarajan NR,
Chairman – JBEGlobal.com Job Portal & IATFTrainingPortal.com (Since 2013) Past – Delphi TVS | Rane | Brakes India |
Iris Mfg. (Shriram Group) | Hinduja Foundries | IRS (IRQS) | 9362439124 | devarajan.jupiter@gmail.com