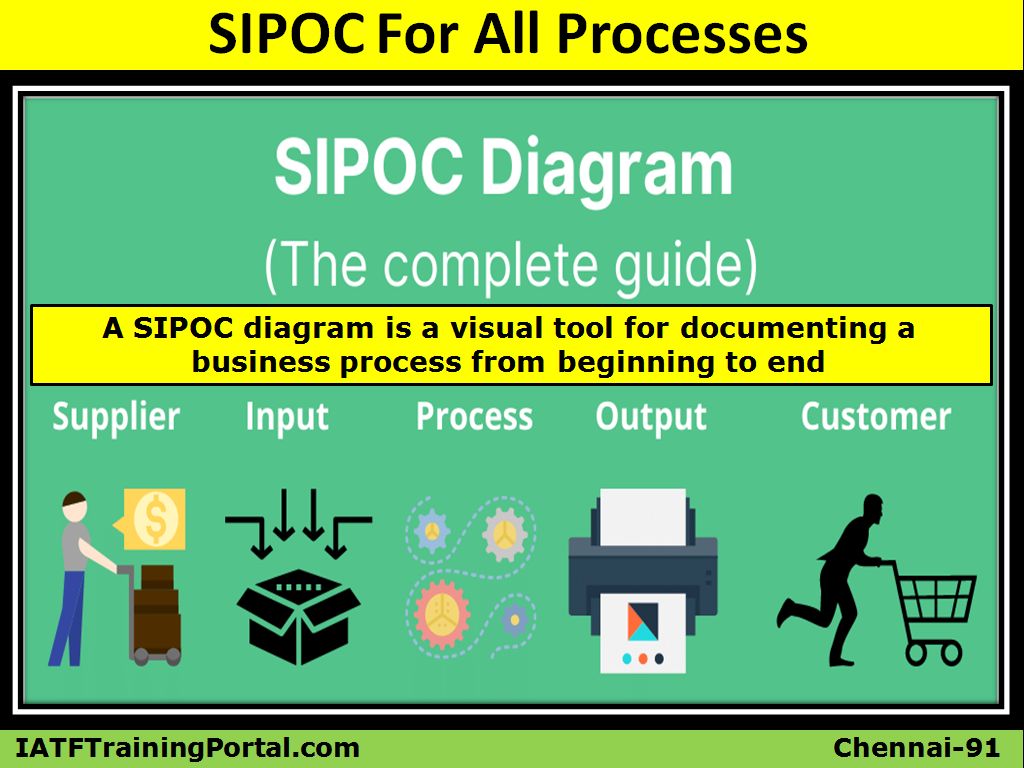
Many of you may be aware of the “Process Flow Diagram (PFD)” which is shown below. A PFD helps in mapping the entire manufacturing process responsible for the product. It maps the manufacturing process steps right from the receipt of raw material, till despatch. This PFD mapping helps to develop the PFMEA & Control plan. This PFD, PFMEA & Control Plan helps in improving the quality (effectiveness) & quantity (efficiency) of the component aiming for zero defects.
Similarly the “Business process flow diagram” or “business mapping” is
vital in improving the effectiveness (quality) & efficiency (profit) of the
business. In many of my articles I have quoted the importance of “the owner
with his team needs to build a perfect business map & review this frequently”.
This article will help in assisting business owners to build a strong “business
process flow diagram” or business map. Such a “Business process flow diagram”
is common for all businesses, it can be done by school, college, hospital, bus
stop (Koyambedu CMBT bus stand is an ISO certified bus stand), hospitals etc.
To build a business map, the owner & his team must have a thorough
understanding about the terms “Activity”, “Process”, “System” &
“Procedure”. See the slide shown below that defines activity, process, system
& procedure. As the sequence suggests, without defining activities
involved, processes cannot be defined properly. Without defining activities
& processes, systems (qms, ems, ohsas etc) cannot be defined properly.
Without defining systems properly, procedures cannot be built perfectly. Once
this understanding is clear the owner & his team can proceed further in
building a self-sustaining, continually improving processes which helps
businesses to reach TQM levels.
SIPOC which is a quick summary of processes (like a ready reckoner)
needs to be understood first, a sample SIPOC is shown below. When all the
processes or departments related SIPOCs are compiled perfectly by adding more
spice to SIPOCs like covering 7M conditions, “Process measures” or “KPI” or
“Process Objectives” etc., it serves as a perfect tool to monitor & control
all the processes (or departments) to bring them to Six Sigma & TQM levels.
Such spicy SIPOC can be called a “Process Analysis Sheet” or “High Level Process
Map” etc.
To help the business community in building perfect SIPOCs / Process
Analysis Sheets, I will be providing samples of around 23 department-wise
SIPOCs / Process analysis sheets in this article. This will help everyone to
understand the concepts as well implement SIPOCs strongly in their existing
businesses.
In building “business process flow diagrams”, mapping the “Sequence
& interaction of processes”, helps in building SIPOCs for all processes or
departments. It gives a basic idea in building activity, process, system &
procedure steps.
A foundry example is taken in the “Sequence & interaction of
processes” slide shown below. Seeing this one can have a broader idea about how
major processes or departments interact with each other. Activity & process
steps can be clubbed department-wise & we can use department concepts for
managing the processes better.
Marketing receives requirements from customers. Marketing forwards it to
“New product development” (called as “Mfg. process design” here) & this team
develops tools & equipment required for the product & conducts trials.
Production team takes over after trials & regular despatches starts. Based
on the product delivery & customer PPM levels, customer satisfaction is
measured & monitored continuously. QC, Purchasing, Stores, Machine
Maintenance, Tool Maintenance, HR, IT, Finance teams provide all the support
required for the successful production & despatch activities of products.
Top Management, MR & Internal audit team ensures all the practices comply
with requirements.
All the processes (or departments) are categorized as “Management
Processes (MP)”, “Customer Oriented Processes (COP)” & “Support Processes
(SP)” as shown in the image. Such categorization helps in prioritizing
processes like risk prioritization in FMEA. COP is first priority, SP is second
priority & MP is third priority. Owners need to concentrate in bringing
COPs to zero error levels first & other processes can be addressed after
that. It is also advisable to outsource partly or fully all the “Support
Processes” which helps the owners to concentrate in bringing zero error on
COPs. Many giant companies have already started outsourcing maintenance, qc, hr
activities. Some partial outsourcing activities are also possible in MP. Such
outsourcing also helps in cost reduction, audit man-days reduction by 3rd
party certification body auditors as their calculation of audit days depends on
head count of clients.
All the SIPOCs shared in this article were derived not only based on
IATF16949, but also considering the QMS requirements of IATF subscribing OEMs
like ASES of Renault Nissan, QSB of General Motors, 5 Star of Hyundai etc.
1) SIPOC Marketing
Let us start with the COP related SIPOCs first. Marketing comes first in
the business process flow mapping as well as in the COP. Seeing the SIPOC of
marketing will make you understand that it is not only a commercial activity,
there are lots of technical activities also involved. If any company or owner
is still seeing marketing as just a commercial activity, it is better to change
their mindset & bring techno commercial or technical persons into
marketing. This will definitely boost the confidence of customers &
internal team involved which will help in increasing sales, profits & productivity.
2) SIPOC Tool Design
Next SIPOC asper business process flow is “Tool design”. Once
commercials are freezed, the marketing team formally announces project
“kick-off” & releases the requirements to all the MP, COP & SP. The
next step is to start designing patterns, tools, core box, jigs, fixtures,
gauges. Tool design team derives a “Timing plan” for the release of designs
& adheres to the plan.
3) SIPOC Tool Manufacturing
Once design team starts releasing the drawings, “Tool manufacturing”
team derives a “Timing plan” for the manufacturing, assembly & trials to
prove the tools. “Tool manufacturing” team starts manufacturing the tools
in-house or outsources some of the tool manufacturing with the help of “process
engg” & “purchasing” team.
4) SIPOC Process Engineering
Process Engineering team derives a “Timing plan” in-line with “APQP”,
actively interacts with all the people involved from project kick-off till the
project handover (sign-off) to production after successful PPAP “Significant
production run”.
5) SIPOC PPC
PPC gets involved by scheduling trial orders by allocating resources
needed for trial runs. PPC increases the schedule gradually once the project
reaches PPAP run stage, ramp-up stage & full volume production stage.
6) SIPOC Sand Preparation
Casting production has 5 major steps: sand, core, moulding, melting
& fettling. Sand preparation is moulding sand preparation in tonnes of
volumes continuously to cater the moulding activities. Moulding sand prepared
is simultaneously checked by QC in the sand lab for 16 parameters for passing
the sand for further processing to the next process of moulding.
7) SIPOC Core Making
Cores are placed inside mould wherever holes, projections, grooves,
recess etc are required in a casting. A single mould or casting may require
multiple cores of various shape, size & core materials. Core shop will be
making such cores & transfer the same to the moulding section.
8) SIPOC Mould Making
Mould is made exactly like the shape of the final casting required with
some additional material that is unavoidable for the success of the process
like runners (to pour molten metal), risers (to ensure enough molten metal is
poured), parting lines etc. Modern mouds consist of only two half, the cope
& drag which is closed after moulding & placing cores in required
places. Moulds are moved on a JIT (Just In Time) conveyor or moved manually to
the next stage.
9) SIPOC Melting & Pouring
Melting happens in traditional style in cupola furnaces or in modern
electric furnaces. Tons of molten metal will be melted continuously & moved
to pouring machines or manual pouring sections. In pouring machines pouring
time can be automated & no need to watch runner riser constantly.
10) SIPOC Fettling
Runner risers & big projections are removed after pouring using
special tools. Casting is allowed to cool for several hours till it comes to
normal room temperature. Fettling is done to bring the casting to the final
shape. Snag grinding is done as a part of fettling to bring castings to the
exact size on the one or the three planes. Shot blasting is done to remove
unwanted sand or foreign particles from the surface.
11) SIPOC Pre-machining
Many casting defects surface when it is machined. Hence the latest
practice of all foundries is to do a pre-machining at their premises itself
which helps to avoid sending defective castings to customers. Pre-machining
brings the casting to the closest required shape & size, leaving only a few
finishing activities to be done by the customer prior to their assembly.
12) SIPOC Warehouse (Finished goods storage &
despatch)
Castings are moved to the warehouse from fettling or pre-machining. All
these castings are packed with adequate preservation with appropriate
identification & dispatched with necessary documents & reports to
customers.
Let us move on to the “Management Process” (MP) related SIPOCs
13) SIPOC Top Management
Top Management declares it Vision, Mission statements. Vision is the
final destiny or the final goal (Egs: World No.1 Foundry), it may take longer
time or even take generations to achieve this Vision. Mission are the next 5
year plan or progress intended which helps to achieve the vision on a longer
run. Vision derives mission & mission is converted into the business plan
for the present year. Top management monitors & ensures the business plan
goals for the year are met. Top Management reviews adequately with all the
process owners on a daily weekly monthly quarterly basis against business plans
& ensures recovery actions wherever the targets are not met.
14) SIPOC MR Functions
Management Representative ensures QMS practices are established,
implemented & maintained which guarantees the Top Management, Customers
& Process owners that the company, its processes & its products are at
its best all the time.
15) SIPOC Internal Audits
Internal audits can be a part of MR functions, or it can be taken care of by a separate team. QMSystem audit, mfg.process audit, product audit & many more audits that are happening more or less on a daily basis in some companies has raised the need to have separate team or atleast one dedicated person with some part time auditors from other processes to handle “Internal Audit” process separately.
Let us move on to the “Support Process” (MP) related SIPOCs
16) SIPOC Purchasing
Mostly purchasing decides make or buy decision. Latest profitable trend
is to make 40% or less & buy 60% or more. This helps to multiply turnover
also without increasing capital expenditure. Making important manufacturing
& assembly activities in-house & buying rest is a successful purchasing
strategy.
17) SIPOC Stores
Storing as little as possible is the trend. Even storing nearer to the
consumption point inside the shop floor is also a viable solution. Smaller
stores help in increasing the profitability.
18) SIPOC Infrastructure
Infrastructure department constructs new buildings, new machines, new
conveyor systems, maintains roads, canteens, electrical, plumbing activities
across the plant.
19) SIPOC Machine Maintenance
Manufacturing industries need to concentrate on machines to bring zero
defects. Hence this function is vital. Machine maintenance takes over
infrastructure built including machines from the infrastructure department
& maintains it. MTBF & MTTR are two vital process indicators that need
to be monitored, measured & improved continuously. TPM also helps in
bringing zero breakdowns as well as trains machine operators to do regular
& minor maintenance activities. This helps production to be less dependent
on the machine maintenance team to run the show 24x7 without any hiccups.
20) SIPOC Tool Maintenance
Tool maintenance is an important function for any foundry or for any
tool dominant processes like sheet metal, plastic injection moulding, thermo-coal
manufacturing units. Foundry activities by its nature have to handle too much
equipment like core boxes, patterns, jigs, fixtures that need regular
servicing, replacement, repair & calibration. Hence it needs a separate
team to handle these activities. In other cases, the machine maintenance team
& production team can handle the maintenance of equipment also apart from
machines.
21) SIPOC Quality Control
Quality control’s job is detection, prevention (QA) is inbuilt into the
NPD process. QC through their incoming, inprocess, final inspection activities
will keep on detecting NC products. Production & NPD must challenge &
encourage QC to try & find NC products. QC will also maintain internal
labs, do calibration & MSA activities apart from inspection.
22) SIPOC Human Resource
HR takes care of employee life cycle during their tenure with the
company, i.e, from joining till resignation. HR also takes care of training of
supervisors & above. Actually the training indicated in IATF or ASES or QSB
insist on adequate training to those who are actually involved in producing
products like operators & casual labourers. Training supervisors &
above do not bring any huge impact on product or process, hence such training
can be limited. More focus needs to be given to training operators & casual
labours. In the SIPOC of production (sand, core, moulding, melting, fettling,
pre-machining) provided above, one can see more focus is given to operator
& casual labour training. Four separate procedures (1)operator training
(2)operator observation (3)refreshment training for operators (4)casual labour
training were assigned to the production department. As these training are too
technical, it is assigned to the production department & they are asked to
take care of these meticulously.
23) SIPOC – Information Technology
The role of IT in a foundry or any factory has a very limited role yet
it is very powerful. They may not be deciding on technical software to be
purchased like Autocad, Catia, software for QMS but their role is vital in
maintaining this software & ensuring no data loss or data theft happens.
Thanks for spending your valuable time here. Keep in touch, keep
following & keep supporting us.
Thanks & Regards,
Devarajan NR,
Chairman – JBEGlobal.com Job Portal
& IATFTrainingPortal.com (Since 2013) Past – Delphi TVS | Rane | Brakes
India | Iris Mfg. (Shriram Group) | Hinduja Foundries | IRS (IRQS) | 9362439124
| devarajan.jupiter@gmail.com