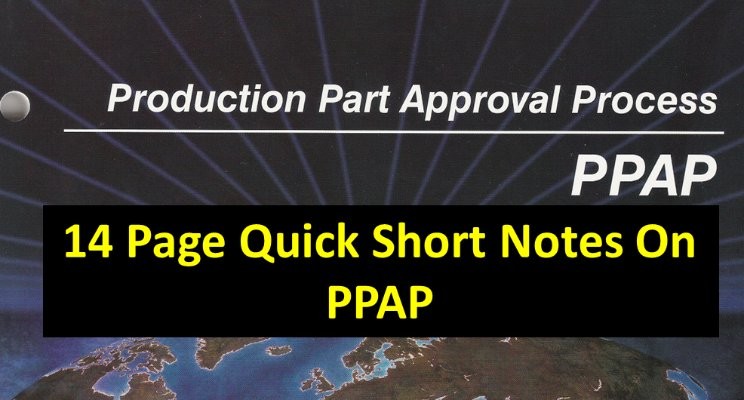
14 Page Quick Short Notes On PPAP
I have taken some quick short notes for PPAP while preparing for TS16949 IATF Auditor Evaluation process. Sharing this to my followers, as it may be useful for someone. I will share other short notes i have taken on core tools one by one.
Thanks for
spending your valuable time here. Keep in touch, keep following & keep
supporting us.
Thanks
& Regards,
Devarajan NR,
Chairman – JBEGlobal.com Job Portal & IATFTrainingPortal.com (Since 2013) Past – Delphi TVS | Rane | Brakes India |
Iris Mfg. (Shriram Group) | Hinduja Foundries | IRS (IRQS) | 9362439124 | devarajan.jupiter@gmail.com
Production Part Approval Process
Before getting into the short notes please see this nutshell which will be helpful in understanding PPAP better.
To have a basic idea about PPAP, you can also visit my another publish using this link https://www.linkedin.com/pulse/ppap-nutshell-devarajan-rajagopalan?trk=pulse_spock-articles
Introduction
Purpose,
1.All customer engineering design record & specification requirements are properly understood,
2.Mfg. process has the potential to produce product consistently meeting these requirements during an actual production run at the quoted production rate.
Applicability,
1.Internal external organization sites supplying,
a) Production parts
b) Service parts
c) Production parts or
d) Bulk materials
2.For bulk materials, PPAP is not required unless specified by the authorized customer representative.
3.Organization supplying standard catalog production or service parts shall comply with PPAP unless formally waived by the authorized customer representative.
Approach,
1.“Shall” indicates mandatory requirements.
2.“Should” indicates a recommendation.
3.“Note” are for guidance in understanding or clarifying the associated requirement.
4.For the purpose of PPAP, the terms & definitions given in ISO/TS16949 & the PPAP glossary apply.
1-General
1.1-Submission of PPAP
1.A new part or product
2.Correction of a discrepancy on a previously submitted part
3.Product modified (by an engg. Change to design, spec or matls.)
4.Any situation required by section 3.
2-PPAP process requirements
2.1-Significant production run
1.Shall be from one hour to eight hours of production. Minimum 300 consecutive parts.
2.Shall be conducted at production site, production rate, production tooling, production gaging, production process, production materials & production operators.
3.Parts from each unique production process (e.g., different lines, cells, cavity, die, mold, tool or pattern) shall be measured & representative parts tested.
4.For bulk materials, no specific number of parts is required.
2.2-PPAP requirements
1.Organization shall meet all specified PPAP requirements (2.2.1 through 2.2.18). Shall also meet all customer-specific PPAP requirements.
2.Parts shall meet all customer engineering design record & specification requirements.
3.If any specifications cannot be met, the organization shall document their problem solving efforts & CA.
2.2.1 – Design record - Organization shall have design record for saleable product & components.
2.2.1.1 – Reporting of part material composition - Shall provide material / substance composition reporting & report complies with CSR.
2.2.1.2 – Marking of polymeric parts - Shall identify with ISO symbols as specified in ISO11469 &or ISO1629 (plastic ≥ 100g & elastomeric ≥ 200g)
2.2.2 – Authorized engineering change documents - Shall have authorized engg. change documents (for those effected in product without changing design record).
2.2.3 – Customer engineering approval - Where specified, orgn. shall have customer engg. approval.
2.2.4 – Design FMEA - Product design responsible organizations shall develop a DFMEA complying with CSR.
2.2.5 – Process flow diagram(s) - Shall have a PFD in orgn format clearly describing production process steps & sequence complying with CSR.
2.2.6 – Process FMEA - Shall develop a PFMEA complying with CSR.
2.2.7 – Control plan - Shall have a control plan that defines all methods used for process control complying with CSR.
2.2.8 – MSA studies - Shall have applicable MSA studies for all new or modified gages, measurements & test equipment.
2.2.9 – Dimensional results - Shall provide evidence for dimensional compliance (for each unique mfg. process egs., cells or production lines & all cavities, molds, patterns & dies) with design record & control plan. Shall identify one of the parts measured as the master sample.
2.2.10 – Records of material / performance test results - Shall have records of material and or performance test results for tests specified on the design record or control plan.
2.2.10.1 – Material test results - Shall perform tests for all parts & product materials when chemical, physical, or metallurgical requirements are specified by the design record or control plan.
2.2.10.2 – Performance test results - Same as 2.2.10.1
2.2.11 – Initial process studies (focus on variables)
2.2.11.1 – General
Shall obtain customer concurrence on the index for estimating initial process capability prior to submission.
Shall perform MSA to understand measurement error.
Short term study should be based on a minimum of 25 subgroups & 100 readings from consecutive parts of the significant production run.
2.2.11.2 – Quality indices
Initial process studies shall be summarized with capability or performance indices, if applicable.
2.2.11.3 – Acceptance criteria for initial study
For process that appear stable,
>1.67 – meets acceptance criteria
1.33 to 1.67 or more – may be acceptable
<1.33 – does not currently meet the acceptance criteria.
2.2.11.4 – Unstable processes
Organization shall eliminate special causes of variation prior to PPAP submission.
2.2.11.5 – Processes with one-sided specifications or non-normal distributions
Shall determine alternate acceptance criteria for processes with one sided specifications or non-normal distributions.
2.2.11.6 – Action to be taken when acceptance criteria are not satisfied
Shall submit for approval a corrective action plan & a modified control plan (normally providing for 100% inspection).
2.2.12 – Qualified laboratory documentation - Inspection & testing for PPAP shall be performed by a qualified laboratory. The qualified lab shall have a lab scope & documentation showing that lab is qualified for the type of measurements or tests conducted.
2.2.13 – Appearance approval report (AAR) - A separate AAR shall be completed for each part or series of parts if the product / part has appearance requirements on the design record.
2.2.14 – Sample production parts - Shall provide sample parts as specified by the customer.
2.2.15 – Master sample - Shall retain a master sample showing customer approval date on the sample. Separate master samples shall be retained of a multiple cavity die, mold, tool or pattern or production process.
2.2.16 – Checking aids - Shall submit with the PPAP any part specific assembly or component checking aid. MSA studies shall be conducted in compliance with CSR.
2.2.17 – Customer-specific requirements - Shall have records of compliance to all customer specific requirements.
2.2.18 – Part submission warrant (PSW)
Upon completion of all PPAP requirements, the organization shall complete the PSW
A separate PSW shall be completed for each customer part number.
2.2.18.1 – Part weight (mass)
Record part weight on PSW in Kgs to four decimal places (used for vehicle weight analysis only).
3-Customer notification & submission requirements
3.1 – Customer notification
1.Shall notify of planned changes to the design, process or site (refer examples in table 3.1).
Other construction or material
New or modified tools (except perishable, std. tools)
Upgrade or rearrangement of existing tooling or equipment.
Tooling & equipment transfer
Change of suppliers for parts, non-equivalent material, or services (eg., heat treating, plating)
Tooling inactive for 12 months or more
Product / process changes (internal or suppliers)
Change in test/inspection method-new technique
New source of raw material (from new or existing supplier) – For bulk materials
Change in product appearance attributes
2.Upon notification & approval, PPAP submission is required after change implementation.
3.2 – Submission to customer
1.Shall submit for PPAP approval prior to first shipment in the following situations,
New part or product.
Correction of a discrepancy on a previously submitted part.
Engineering change
Process technology new to the organization, not previously used for this product – for bulk materials
4-Submission to customer – levels of evidence
4.1 – Submission levels
1.Levels,
Level-1 – Warrant & AAR
Level-2 – Warrant, samples & limited supporting data
Level-3 – Warrant, samples & complete supporting data
Level-4 – Warrant & other requirements as defined by customer
Level-5 – level-3 reviewed onsite
2.Level-3 is the default level
3.Minimum submission requirements for bulk materials is the PSW & the “Bulk Materials Checklist”
5-Part submission status
5.1 – General
1.Upon approval of the submission, the organization shall assure future production continues to meet all customer requirements.
5.2 – Customer PPAP status
1)5.2.1 – Approved – Meets all requirements. Can ship subject to release.
2)5.2.2 – Interim approval – Permits shipment for limited time or quantity.
3)5.2.3 – Rejected – Not meeting requirements (lot or documentation).
6-Record retention
PPAP records shall be retained for the length of the time that the part is active plus one calendar year
PPAP gap analysis for superseded part PPAP file to identify document / record to be carried forward.
Appendix-A-Completion of the part submission warrant (PSW)
PSW contains,
1.Part information
2.Organization manufacturing information
3.Customer submittal information
4.Materials reporting
5.Reason for submission
6.Submission level
7.Submission results
8.Declaration
9.For customer use only
Appendix-B-Completion of the appearance approval report (AAR)
Appendix-C-Production Part Approval, Dimensional Results
Appendix-D-Production part approval, material test results
Appendix-E- Production part approval, performance test results
Appendix-F-Bulk Material – Specific Requirements
F.1-Introduction
1. Guidance or comply this appendix for bulk material PPAP.
F.2-Applicability
1.Examples of bulk material include, but are not limited to,
a)Adhesives & sealants
b)Chemicals
c)Coatings
d)Engine coolants
e)Fabrics
f)Film & film laminates
g)Ferrous & non-ferrous metals
h)Foundry
i)Fuels & fuel components
j)Glass & glass components
k)Lubricants
l)Monomers, pre-polymers & polymers
m)Performance fluids
F.3-Bulk materials requirements checklist
1.For bulk material, the PPAP elements required are defined by the bulk materials requirements checklist.
F.4-Design matrix
1)F.4.1-Introduction
a)Organizations supplying bulk materials generally deal with chemistry & functionality of the product.
b)Design matrix shall be developed prior to Design FMEA. Design matrix correlates customer expectations with the product design items.
c)Design matrix determines complex interactions of,
i.Formula ingredients
ii.Ingredient characteristics
iii.Product characteristics
iv.Process constraints
v.Conditions for customer uses
d) High impact items can be then analyzed in Design FMEA
2) F.4.2-Design matrix – elaboration
a)Constructing design matrix,
i.List the functions (desired attributes / potential failure modes) in horizontal axis (rows)
ii.List the design items (formula, ingredient, product, process, conditions) as potential causes
iii.For each design items, enter the current robust threshold range levels & units
iv.Correlate the potential causes to the potential failure modes using a number, letter or symbol representing the impact or strength of the relationship. Ask what would happen if a potential cause item is allowed to go under or over its robust minimum or maximum, respectively
v.After completion of the rankings in the design matrix, review the category / characteristics for a preliminary assessment of special characteristics. Designate any special characteristics in the column-1.
vi.The high negative impact potential causes are transferred to the Design FMEA for anlaysis.
F.5-Design FMEA
1) F.5.1-Effects of failure & severity rankings
a)List effects of failure
i.Consumer effects
ii.Customer effects
b)Assign a severity ranking to each effect (use FMEA manual & develop own scale to match the situation)
2) F.5.2-Potential cause(s) / mechanisms of failure & design matrix
a)From design matrix, list the high negative impact characteristics as potential causes/mechanisms of failure which are associated with potential failure modes.
b)Mechanisms are generally described as over or under a certain threshold. These thresholds define the boundaries of the product approval & subsequent requirements of change notification.
3) F.5.3-Likelihood of occurrence rankings
a)Use occurrence matrix recommended which is based upon observed evidence the formulator has in the design.
4) F.5.4-Current design controls
a) Supplementing the FMEA manual, bulk material design controls may also include,
i.Designed experiments (DOE)
ii.Customer validation tests & trial runs
iii.Test protocols
iv.Variation of supplier specifications
v.Formulating practice robust changes
b) Design controls identified by a number should be available so that the relevant content of that control can be understood.
5) F.5.5-Likelihood of detection rankings
a) Use detection matrix recommended which is based upon the assessed testing method R&R’s percentage of specification range & the quality of evidence.
F.6-Process FMEA
1.Severity, occurrence & detection rankings listed.
F.7-Special characteristics
1) F.7.1-Introduction
2) F.7.2-Special characteristics – elaboration
a) Flow of potential special characteristic through supply chain is demonstrated.
F.8-Control plan
1) F.8.1-Introduction
a) Bulk material control plan serves as a mechanism to,
i. Highlight special product / process characteristics & their controls
ii. Link together sources of control methods, instructions & specification / tolerance limits & reference them in one document.
2) F.8.2-Control plan – elaboration
a) Proto, prelaunch & production control plans explained.
F.9-MSA studies
1.Bulk materials often require further processing after sampling in order to make a measurement.
2.Measurements are often destructive in nature & this prevents retesting the same sample.
3.In process industries measurement may account for 50% or more of the total observed variation.
4. MSA studies are not required where standardized tests are used (still important to understand measurement component of variation in test method).
5.Any MSA studies should be applied to each test method associated with special characteristics, and not to each individual product measured by the test method. Therefore MSA studies should be conducted as broadly as possible across all products which use a particular test method. If the resulting variability is unacceptable, then either the studies should be conducted on a narrower class of products or action should be taken to improve the test method.
F.10-Initial process studies for special characteristics
1. Have to be done carefully due to the following nature of process industries,
a) Span a variety of production processes
b) Produced in small quantities (no more than once or twice per year)
c) Production process already in place before testing sufficient samples
d) Frequent change in personnel and/or equipment
e) Numerous input variables, many control variables & a variety of product variations.
f) There are non-linearities (doubling input will not double output).
g) Effects & relationships between variables & controls are also not usually known without error.
h) Multiple processes are usually interconnected, sometimes with feedback loops.
i) There are also timing considerations & delays in reaction time.
j) In many cases correlated variables must be used (measurements of component variables are generally less precise).
F.11-Master sample
1. F.11.1-Introduction
a) Shall be agreed by customer & organization.
b) Physical sample can be retained if physical or chemical properties will not change for decades (stable & unchanging over an extended period of time).
c) Analytical sample record can be maintained when sample change with time, but can be precisely quantified by appropriate analytical techniques (e.g., ultra-violet or infra-red spectra “fingerprint”, atomic absorption or gas chromatographic-mass spectrometric analysis).
d) Manufacturing sample record should be generated when bulk materials cannot be distinctly identified or change over time.
2. F.11.2-Paint manufacturing master sample record – examples
a) Paint mfg. master sample record – batch/lot mfg. record
b) Paint mfg. master sample record – product test results
c) Paint mfg. master sample record – certificate of analysis ingredients
F.12-Part submission warrant (CFG-1001)
1. Shall be submitted when PPAP for bulk materials is applicable.
2. Self certified suppliers can sign in PSW & forward that to customer.
F.13-Interim approval
1. Bulk material interim approval form
F.14-Customer plant connection
1. F.14.1-Customer’s responsibilities
a) Shared responsibility
b) Three key components of the customer plant connection are the development of,
i. Customer process matrix
ii. Determination of special characteristics from the customer process matrix
iii. Preparation of a control plan
For bulk materials, conducting the steps outlined in this “customer plant connection” is highly recommended.
2. F.14.2-Customer plant connection-clarification
a) Applicable to materials that are transformed from bulk (e.g., wet can of paint) to final product (e.g., cured paint film), may not apply to all bulk (e.g., washer fluid, engine oil)
b) Both bulk product characteristics & final product attributes may be impacted by customer process controls.
c) The process steps at customer plants may be matrixed versus the special characteristics. Where high impact is evident, those process steps may be analyzed by the PFMEA methodology.
d) The special characteristics may then be determined, & be included in a control plan for customer process. These special control characteristic items may be monitored & continuously improved.
3. F.14.3-Customer plant connection guidelines
a) 11 steps discussed on developing “Customer process matrix” with an example
Appendix-G-Tires– Specific Requirements
G.1-Introduction & applicability
G.2-Guidelines for PPAP requirements
1. Significant production run
a) Minimum 30 tires
b) PPAP is not required for additional molds that are brought on line in the approved production process. All additional molds shall be certified by the organization’s internal certification criteria & documentation.
2. Material test results
a) Testing is applicable only to finished tires & not to raw materials. Tire industry practice does not require chemical, physical, or metallurgical testing. Material test results are not required for PPAP.
3. Special characteristics
a) Tire uniformity (force variation) & balance are designated special characteristics.
4. AAR – Not applicable
5. Master samples – not retained
6. Process flow diagrams – See PPAP 2.2.5
7. Checking aids – not required.
8. PPAP submission warrant
a) Reporting of multiple cavities, molds, lines etc. on the PSW is not required for tires.
9. Part weight (mass)
a) PPAP tires are weighed to two (2) significant decimals. The average is reported on the PSW to four (4) decimals.
G.3-Submission to customer-Levels of evidence
1. Retention / submission requirements (reference table 4.2)
a) Records of items submitted (S) & retained (R) are maintained at appropriate locations designated by the organization.
Appendix-H-Truck industry– Specific Requirements
Introduction
Applicability (see page 1)
1. Customer has the right to request a PPAP at any time to re-qualify a production component.
2. Feature base process or part number generated components are PPAP qualified using the highest content configuration to qualify the master part number. All other configurations may be approved with the submission of a PSW linking the new part number with the master part number.
3. For bulk material & standard catalog parts, the organization shall formally qualify product to their design record & submit a PSW when requested by customer.
Significant production run (see 2.1)
1. Adequate parts be manufactured during this run to confirm the quality & capability. For low volume applications, sample sizes 30 piece may be utilized for preliminary process capability studies.
2. When 30 samples are not attainable prior to production, interim PPAP may be granted. A 100% inspection of special characteristics is required during interim period.
Dimensional results (see 2.2.9)
1. Dimensional results to match with marked-up drawings.
Material test (see 2.2.10.1)
1. The organization shall also submit a completed DVP&R that summarizes appropriate performance & functional test results.
Quality Indices (see 2.2.11.2)
1. When the customer specifies special characteristics & the estimated annual volume is less than 500, the control plan shall contain,
a) Perform 100% inspection & record the results (or)
b) Conduct an initial process capability study with a minimum of 30 production pieces & maintain SPC control charts of the characteristics during production.
2. For special characteristics that can be studied using variables data, the organization shall utilize one of the following techniques to study the stability of the process,
a) Xbar & R charts, n=5, plot minimum 6 subgroups (or)
b) Individual X-Moving Range, plot minimum 30 data points.
Master sample (see 2.2.15)
1. Shall be retained after PPAP approval when specified by the customer.
Part submission warrant (see 2.2.18)
1. When specified, use truck industry PSW.
Part weight (mass) (see 2.2.18.1)
Atleast one part shall be from each cavity, tool, line, or process used in product realization.
Customer notification (see 3.1)
Completion of PSW
1. Part information
2. Organization manufacturing information
3. Submission information
4. Reason for submission
5. Requested submission level
6. Declaration
7. For customer use only – leave blank
8. Completion of the product / process change notification
Glossary
Following definitions given,
1. Accredited laboratory – reviewed & approved by nationally recognized accreditation body, or as an alternative, a customer recognized accreditation body (conforming to ISO/IEC guide 58 of calibration or test laboratory accreditation to ISO/IEC 17025, or national equivalent).
2. Active part – currently being supplied for original equipment or service applications.
3. Appearance item – visible once the vehicle is completed.
4. Approved – used in PPAP to mean that the parts, materials, & and/or related documentation meet all customer requirements.
5. Approved drawing – an engineering drawing signed by the engineer & released through customer’s system.
6. Approved materials – governed either by industry standard specifications or by customer specifications.
7. Approved source list – list of organizations & suppliers that have been found acceptable to the customer.
8. Attribute data – qualitative data that can be counted for recording & analysis.
9. Authorized customer representative(s) – is the individual or individuals having approval authority on behalf of the customer.
10. Black box – refers to a part where design responsibility belongs to the organization or the supplier. ODD (outside design & development) has the equivalent meaning.
11. Bulk material – is a substance (non-dimensional solid, liquid, gas) such as adhesives, sealants, chemicals, coatings, fabrics, lubricants, etc.
12. Bulk materials requirements checklist – defines customer PPAP requirements for bulk material.
13. CAD/CAM math data – is a form of design record by which all dimensional information necessary to define a product is conveyed electronically.
14. Calibration – is a set of operations which compares values taken from a piece of IMTE or a gage to a known standard under specified conditions.
15. Capability – total range of inherent variation in a stable process.
16. Checked print – is a released engineering drawing with actual measurement results recorded by the organization adjacent to each drawing dimension & other requirements.
17. Conformance – part or material meets customer’s specifications & requirements.
18. Control – see statistical control
19. Control charts – see the statistical control reference manual.
20. Control plans – written descriptions of the system for controlling production parts, bulk materials and processes.
21. Customer – recipient of the organization’s or supplier’s product or service.
22. Design-intended robust range – limits within which parameters may be allowed to vary while still ensuring that a product complies with fitness for use.
23. Design record – is the part drawing, specifications, and/or electronic (CAD) data used to convey information necessary to produce a product.
24. Failure mode & effects analysis (FMEA)
25. Initial process study – see SPC manual
26. Laboratory – test facility that may include chemical, metallurgical, dimensional, physical, electrical, reliability testing or test validation.
27. Laboratory scope – is a quality record containing,
a) Specific tests, evaluations & calibrations that an organization’s laboratory has the ability & competency to perform
b) List of equipment which it uses to perform the above
c) List of methods & standards to which it performs the above
28. Marked print – modified, signed & dated by the customer engineer.
29. Organizations – are providers of,
a) Production materials
b) Production or service parts
c) Assemblies or
d) Heat treating, welding, painting, plating or other finishing services
30. Part submission warrant (PSW) – is an industry standard document required for all newly-tooled or revised products in which the organization confirms that inspections & tests on production parts show conformance to customer requirements.
31. Perishable tools – are drill bits, cutters, inserts, etc. used to produce a product & which are consumed in the process.
32. Process – is a set of interrelated or interacting activities which transforms inputs into outputs.
33. Process flow diagram – is a schematic representation of the process flow.
34. Production environment – all of the process conditions surrounding or affecting the manufacture & quality of a part or product.
35. Production material – material which has been issues a production part number by the customer & is shipped directly to the customer.
36. Production part – manufactured at the production site using production tooling, gaging, process, materials, operators, environment, & process settings (eg.: feeds speed cycle times pressures temperatures)
37. Production part approval submission – specific quantities taken from significant production run made in production environment submitted for approval.
38. Production rate – is the agreed upon no. of parts produced in a planned time period to meet customer assembly or mfg. plant production volume requirements (with consideration of other product mix & machine availability).
39. Quality indices – measures of capability or performance for either product or process.
40. Quality planning – structured process for defining methods (measurements, tests) that will be used in the production of a specific product or family of products. Embodies the concepts of defect prevention & continual improvement as contrasted with defect detention.
41. Quality record – is a document stating results achieved or providing evidence of activities performed.
42. Regular production tooling – tooling with which the manufacturer intends to produce production product.
43. Saleable product/part – specified on the contract between the customer & organization.
44. Significant production run – see PPAP 2.1
45. Site – location at which value added manufacturing processes occur.
46. Special characteristics – product or process parameters which can affect safety or compliance with regulations, fit, function, performance or subsequent processing of a product.
47. Specification – document stating requirements.
48. Stable processes – processes that are in statistical control.
49. Statistical control – all special causes eliminated.
50. Submission level – refers to level of evidence required for PPAP submission.
51. Suppliers
52. Tool – used in process machinery to transform raw material into finished part or assembly.
53. Validation – confirmation through objective evidence that the requirements for a specific intended use or application have been fulfilled.
54. Variables data – quantitative data
55. Verification – confirmation through objective evidence that specific requirements have been fulfilled.
56. Warrant – See PSW.