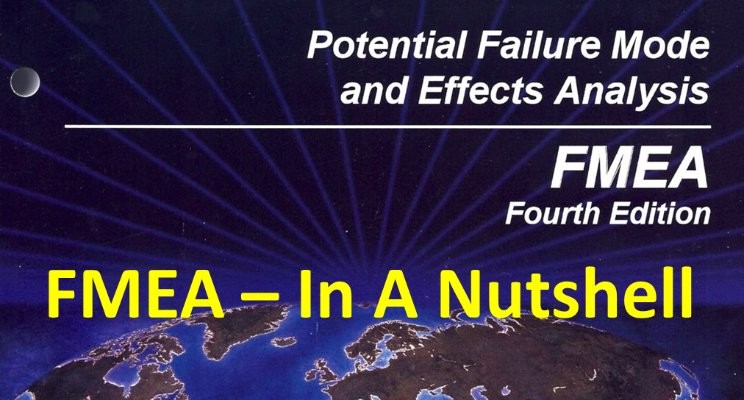
FMEA - In A Nutshell
Already i have shared the following nutshells; those who are interested can click the links below & read those,
- MSA nutshell
- APQP nutshell
- PPAP nutshell
I started preparing nutshells for tougher subjects. Most of the nutshells will be in one slide. FMEA is a higher level subject, hence I was unable to make a nutshell for this in a single slide. FMEA nutshell will be in three slides. In the below write-up I have added four more slides to give a better understanding on FMEA. Here you go.
There are 100+ quality tools available & in use. You must have a clear practical implementation oriented understanding about all these quality tools. You must also know which tool to be used in which sort of situation. Using right tools at right situation with right data will surely solve your existing problem & take your process to next level. Such a continuous endless effort will take your processes, product & your organization to TQM level for sure. Below slide will give you an idea about various quality tools, categorized into three levels Basic, Intermediate & Advanced.
Though there are 100+ quality tools available, only five tools are considered as “Core tools” by IATF & AIAG. You can use many quality tools, but without these five core tools your implementation will not be complete. You can also obtain greater results by practicing only these five tools alone in spirit. IATF/AIAG have released separate manuals for all these five core tools to support implementation. Below slide gives you the details of those five manuals.
Prior to going into the nutshell, have a look at the history or evolution of FMEA. FMEA has a long history dating back to 1949. Initially it was used by teams involved in high level projects where even small mistakes will cost huge - money-wise & reputation-wise. Ford brought FMEA from US Army, NASA to “Automobile industry” after the “Pinto affair”. Pinto affair brought a big setback to Ford money-wise & reputation-wise. AIAG brought FMEA to all automobile suppliers. Now FMEA is widely used in almost all industries.
Now let us jump into the first slide of FMEA Nutshell. This slide gives an outline about types of FMEAs, three criteria for rating (SOD), Risk PN (priority number), threshold value (fixing minimum RPN value for taking further action). Interestingly I guess many people, even experts may not be aware that there is something called “Reverse FMEA”. Yes there is “Reverse FMEA” & GM recommends it through their QSB ("Quality System Basics" Standard). Ford suggests machinery, environment & software FMEAs, this may also may be new to some people.
Second slide clarifies you on “Why threshold value is discouraged?” Seeing these 15 combinations which give the same RPN value of 360, you can understand the major setback in the entire FMEA system. So organization & CFT must be clear on how they prioritize actions for failure modes.
Slide three gives an idea about alternate risk prioritization methods like “arithmetic combination of SOD, SD”. Again this method also have limitations which is explained through three different RPN, SOD & SD combinations.
FMEA if done properly, after adequate understanding, in-spirit will surely give expected results. FMEA is a never ending activity & FMEA is a living document.
FMEA need to be revised or revisited whenever there is change in product, process, process flow, logistics, measurement systems, suppliers, and when process becomes unstable, based on internal / external rejections & feedback.
If FMEA is respected, it will surely take your rejection levels to zero ppm. Below slide gives an awareness about what happens if there is no zero ppm.
Thanks & Regards,