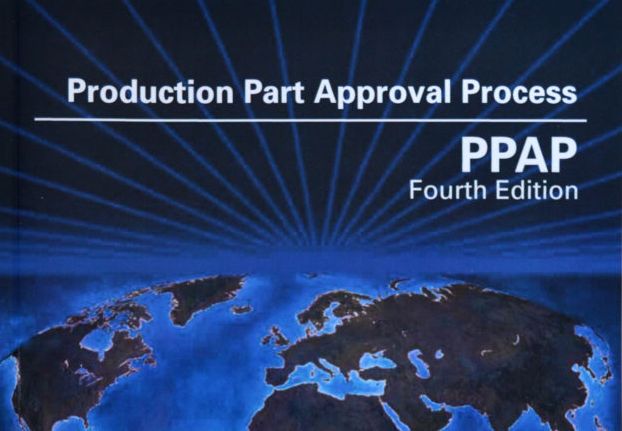
IATF16949 is the most stringent QMS standard presently available.
IATF16949
recommends the usage of 5 core tools, these core tools have separate manuals as
below,
1)
APQP – Advanced Product Quality Planning – 107 page manual
2)
PPAP – Production Part Approval Process – 68 page manual
3)
FMEA – Failure Mode & Effect Analysis – 141 page manual
4)
MSA – Measurement System Analysis – 232 page manual
5)
SPC – Statistical Process Control – 221 page manual
Reading
all these stuff, then trying to understand the concept, logic & maths
behind these are quite difficult & it takes a longer time. Again the time
taken varies person to person considering their age, qualification, experience
& passion. After understanding, implementing these, is again a challenging
task.
To
support everyone who is interested in these subjects, i have developed
“Nutshells” that will give a bigger picture. With this attaching some important
"Nutshells".
Let
us dive-in further into PPAP in this article.
So,
What is PPAP?
Once
a supplier is ready with the product & (mfg.) process design, they will run
the product for the first time. This run is called as “Significant Production
Run”. This run will be kept as small as possible to minimize losses, at the
same time as big as possible to understand the capability & capacity
(through statistics & projection).
PPAP
recommends “300 pieces” or “8 hours production volume” or “volume as-per the
discretion of the customer” for this “Significant Production Run”
During
this run, customer cannot be at your premises & monitor how the progress
happens to ascertain the supplier’s capability & capacity. Hence PPAP
guides the suppliers on conducting such a “Significant production run” and
submit “Parts produced” during this run, along-with “certain documents”.
Customer
can clearly understand the supplier’s capability & capacity by evaluating
the parts and the documents submitted to them. Such an evaluation will help the
Customers to decide on the further course of action.
Further
course of actions can be,
1)
Rejecting the PPAP submitted & request for a re-submission
2)
Interim approval (run with some deviations)
3)
Accepting the PPAP
Then,
how do you know, what documents you need to submit along-with parts?
Customer
will inform a submission level, ranging from one (1) to five (5). If nothing is
informed by the customer, the default level is three (3).
Submission
level three (3) means, that you have to submit all the 18 documents, as
prescribed in the PPAP manual. There will be some documents “Not applicable” to
you, considering the “type of product” & “design responsibility”. If you
are not responsible for the "product design", straight-away first
four documents are “not applicable” to you. If the parts you supply is not an
“appearance item”, then “appearance approval report” (AAR) is not applicable to
you. Any item that is visible to the naked eye of end user / buyer is an
appearance item (Egs: Fuel tank in motorbikes, Car doors)
Customer
may demand Level-5 for highly stable & reliable suppliers (no need to
submit anything with parts, need to retain everything at supplier premises).
See
the below nutshell that details all the eighteen documents & some key
aspects of PPAP.
Beginners
can use this to have an overall idea prior to drill deep. Experts can use this
as a ready reckoner.
My
nutshell on other complicated subjects will be published one by one.
Keep
in touch & keep following.
Thanks,
Devarajan NR,
Chairman – JBEGlobal.com Job Portal & IATFTrainingPortal.com (Since 2013) Past –
Delphi TVS | Rane | Brakes India | Iris Mfg. (Shriram Group) | Hinduja
Foundries | IRS (IRQS) | 9362439124 | devarajan.jupiter@gmail.com