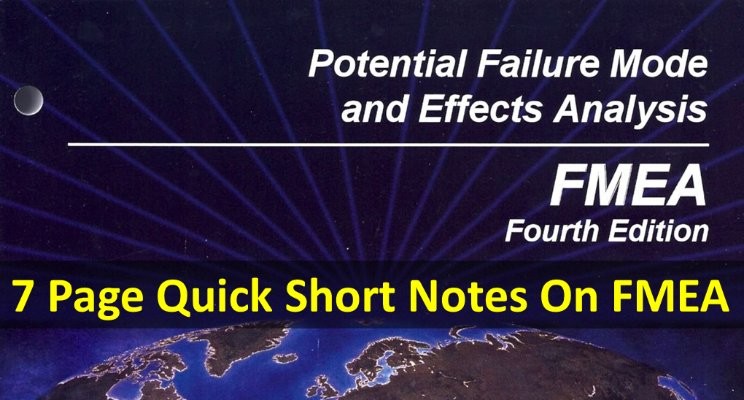
7 Page Quick Short Notes On FMEA
I have taken some quick short notes for FMEA while preparing for TS16949 IATF Auditor Evaluation process. Sharing this to my followers, as it may be useful for someone.
Already i have shared the following quick short notes, those who are interested can click below link & read those,
- 11 Page Quick Short Notes On TS16949 Requirements
- 6 Page Quick Short Notes On APQP
- 14 Page Quick Short Notes On PPAP
Potential failure mode & effect analysis (FMEA)
1-General FMEA guidelines
Introduction
1. FMEA process
a) Is an analytical methodology used to ensure that potential problems have been considered & addressed throughout the product & process development (APQP). Its most visible result is the documentation of the collective knowledge of cross-functional teams.
b) Part of the evaluation & analysis is the assessment of risk.
c) Each FMEA should ensure that attention is given to every component within the product or assembly. Critical & safety related components or processes should be given a higher priority.
d) FMEA success depends on timeliness, it is meant to be a “before-the-event” action, not an “after-the-fact” exercise.
e) FMEA could be used to analyze risk in an administration process or the evaluation of a safety system.
2. Purpose of manual
a) Three basic cases where FMEA can be applied,
i. New design, new technology or new process
ii. Modification to existing design or process
iii. Usage of an existing design or process in a new environment, location, application, or usage profile
3. Scope of manual
Focus on those applications prevalent within automotive industry & its suppliers.
Impact on organization & Management,
1. Important to FMEA development is a process owner & senior management commitment.
2. Ultimately, management has the responsibility & ownership for development & maintenance of the FMEAs.
FMEA explained,
1. The APQP reference manual shows DFMEAs as an activity in the product design & development section and PFMEAs in the process planning & development section.
2. The FMEA analysis should not be considered a single event, but a long term commitment.
3. Clear statements, concise terminology & focus on the actual effects are key to the effective identification & mitigation of risk issues.
Follow-up & continuous improvement,
1. A thoroughly thought-out & well developed FMEA will be of limited value without positive & effective preventive / corrective actions.
2. The FMEA is a living document & should always reflect the latest level, as well as the latest relevant actions, including those occurring after the start of production.
2-Overview of FMEA strategy, planning & implementation
Introduction,
1. FMEA development uses a common approach to address,
a) Potential failure to meet expectations
b) Potential consequences
c) Potential causes (of the failure mode)
d) Application of current controls
e) Level of risk
f) Risk reduction
Basic structure,
1. Fundamentally the format utilized should address:
a) Functions, requirements & deliverables
b) Failure modes (when functional requirements are not met)
c) Effects & consequences (of the failure modes)
d) Potential causes of the failure mode
e) Actions & controls (to address the cause of the failure mode) and
f) Actions to prevent recurrence (of the failure mode)
Approach,
1. There is no single or unique process for FMEA development, however there are common elements as described below,
a) Identify the team
b) Define the scope – following may assist in defining scope,
i. Functional model
ii. Block diagrams
iii. Parameter (P) diagrams
iv. Interface diagrams
v. Process flow diagrams
vi. Interrelationship matrices
vii. Schematics
viii. Bill of materials (BOM)
System FMEA – Chasis sytem, powertrain system, interior system etc.
Sub-system FMEA – Front suspension sub-system which is a subset of the chasis system.
Component FMEA – a brake pad is a component of the brake assembly, which is a subsystem of the chasis system.
c) Define the customers (End user, OEM, supply chain, regulators (Govt.))
d) Identify functions, requirements & specifications
e) Identify potential failure modes
f) Identify potential effects
g) Identify potential causes
h) Identify controls
i) Identifying & assessing risk
j) Recommended actions & results
Management responsibility
3-DFMEA
Introduction
The DFMEA is a living document & should,
a) Be initiated before design concept finalization
b) Be updated as changes occur or additional information is obtained throughout the phases of product development
c) Be fundamentally completed before the product design is released, and,
d) Be a source of lessons learned for future design iterations.
1. Customer defined – End user, OEM, supply chain & regulators (Govt.)
2. Team approach – Developed & maintained by a multi-disciplinary team typically led by the design responsible engineer.
3. Mfg. assembly & serviceability considerations
Development of a design FMEA
Can be mapped to the customer or organization’s product development process
1. Prerequisites – following tools may be applied as appropriate, to assist the team in developing the DFMEA,
a) Block (boundary) diagrams
b) Parameter (P) diagrams – Physics related to function of design
c) Functional requirements – General, safety, Govt. regulations, reliability, loading & duty cycles, quiet operations, fluid retention, ergonomics, appearance, packaging & shipping, service, design for assembly & design for manufacturability
d) Other tools & information sources – schematics, drawings, bill of materials, interrelationship matrices, interface matrix, quality function deployment, quality & reliability history
Example DFMEA
1. Header of the design FMEA form (fields A-H)
a) FMEA number (A)
b) System, subsystem or component name & number (B)
c) Design responsibility (C)
d) Model year / program (D)
e) Key date (E)
f) FMEA dates (F)
g) Core team (G)
h) Prepared by (H)
2. Body of the DFMEA form (fields a-n)
a) Item / function / requirements (a)
b) Potential failure mode (b) – “observed” or “external” effect
c) Potential effects of failure (c)
d) Severity (S) (d)
i) Suggested evaluation criteria
e) Classification (e)
f) Potential cause / mechanism of failure mode (f)
g) Occurrence (O) (g)
i. Suggested evaluation criteria
h) Current design controls (h) – Prevention & detection
i) Detection (D) (i)
i. Suggested evaluation criteria
ii. Determining action priorities
Initial focus should be towards failure modes with high severity rankings
j) Risk evaluation; risk priority number (RPN) (j)
i. RPN = SxOxD (can range from 1 to 1000). The use of an RPN threshold is NOT a recommended practice for determining the need for actions. Another concern with using the threshold approach is that there is no specific RPN value that requires mandatory action.
k) Recommended action (k)
i. To reduce severity (S) ranking: only a design revision can bring about a reduction in severity ranking
ii. To reduce occurrence (O) ranking: by removing or controlling one or more of the causes or mechanisms of the failure mode through a design revision. Actions such as but not limited to the following should be considered,
§ Error proof the design to eliminate the failure mode
§ Revised design geometry & tolerances
§ Revised design to lower the stresses or replace weak components
§ Add redundancy
§ Revised material specification
iii. To reduce detection (D) ranking: The preferred method is the use of error / mistake proofing. Following should be considered,
§ Design of experiments
§ Revised test plan
l) Responsibility & target completion date (l)
m) Actions taken & completion date (m)
n) Severity, occurrence, detection & RPN (n)
Maintaining DFMEAs
1. Should be reviewed whenever there is a product design change & updated as required.
2. Periodic reviews of the rankings, specific focus to O & D rankings.
Leveraging DFMEAs
Linkages
1. Design verification plan & report (DVP&R) – DFMEA & DVP&R have an important linkage. DFMEA identifies “what” while DVP&R provides “how”
2. PFMEA – another important linkage is between DFMEA & PFMEA
4-PFMEA
Introduction
1. Supports mfg.process development in reducing the risk of failures. PFMEA is a living document & should,
a) Be initiated before or at the feasibility stage
b) Be initiated prior to tooling for production
c) Take into account all mfg. operations from individual components to assemblies
d) Include all processes within the plant that can impact the mfg. & assy operations such as shipping, receiving, transporting, storage, conveyors or labeling.
2. Early review & analysis of new or revised processes is advised
3. PFMEA assumes the product as designed will meet the design intent
4. PFMEA does not rely on product design changes to overcome limitations in the process.
Customer defined
Normally be the End user, can also be a downstream operation, a service operation or regulator (Govt.)
Team approach
PFMEA is developed & maintained by a multi disciplinary team typically led by the responsible engineer. Team leader involves all representatives from affected areas.
Design considerations
design opportunities in reducing risk being feedback to design engineer.
Development of a process FMEA
1. Begins by developing a list of what process is expected to do & what not to do (i.e., the process intent), a flow chart of general process with product/process characteristics associated with each operation.
Prerequisites – Process flow diagram
1. PFD & link to PFMEA
a) A preliminary risk assessment using the process flow diagram may be performed to identify which of these operations or individual steps can have an impact on the product mfg. & assy. & should be included in the PFMEA.
b) In order to assure continuity, it is highly recommended that the same cross-functional team develop the PFD, PFMEA & CP.
2. Other tools & information sources
To capture requirements of the process,
a) DFMEA
b) Drawings & design records
c) Bill of process
d) Interrelationship (characteristics) matrix
e) Internal & external non-conformances (known failure modes based on historical data)
f) Quality & reliability history
3. Research information
Review should include,
a) Lessons learnt from previous product & process design
b) Established best practices (guidelines & standards, standard part identification, or error-proofing methods)
c) Quality performance information available from similar previous product & process designs, including items such as,
i. Process yield
ii. First time capability
iii. Parts per million (PPM)
iv. Process capability indices (Cpk & Ppk) &
v. Warranty metrics
§ After considering the above pre-requisites start filling the PFMEA form
Example PFMEA form,
1. Header of the PFMEA form (A-H)
a) FMEA number (A)
b) Item (B)
c) Process responsibility (C)
d) Model year / program (D)
e) Key date (E)
f) FMEA date (F)
g) Core team (G)
h) Prepared by (H)
2. Body of the PFMEA form (fields a-n)
a) Process step / process function / requirements (a)
b) Potential failure mode (b) – “observed” or “external” effect
c) Potential effects of failure (c)
d) Severity (S) (d)
i. Suggested evaluation criteria
e) Classification (e)
f) Potential cause / mechanism of failure mode (f)
g) Occurrence (O) (g)
i. Suggested evaluation criteria
h) Current process controls (h) – Prevention & detection
i) Detection (D) (i)
i. Suggested evaluation criteria
ii. Determining actions priorities
§ Initial focus should be towards failure modes with high severity rankings
j) Risk evaluation; risk priority number (RPN) (j)
i. RPN = SxOxD (can range from 1 to 1000). The use of an RPN threshold is NOT a recommended practice for determining the need for actions. Another concern with using the threshold approach is that there is no specific RPN value that requires mandatory action.
k) Recommended action (k)
i. To reduce severity (S) ranking: only a design or process revision can bring about a reduction in severity ranking
ii. To reduce occurrence (O) ranking: Removing or controlling one or more of the causes of the failure mode through a product or process design revision.
iii. To reduce detection (D) ranking: Redesign of the detection methodology may result in reduction. Increasing frequency of inspection is usually not an effective action. Process can be evaluated by,
§ Results of process DOE or other testing
§ Modified PFD, floor plan, work instructions or preventive maintenance plan
§ Review of equipment, fixtures or machinery specifications
§ New or modified sensing / detection device
l) Responsibility & target completion date (l)
m) Actions taken & completion date (m)
n) Severity, occurrence, detection & RPN (n)
Maintaining PFMEAs
1. Should be reviewed whenever there is a product or process design change & updated as required.
2. Periodic reviews of the rankings, specific focus to O & D rankings.
3. Additional reviews when field issues or production issues, such as disruptions
Leveraging PFMEAs
Linkages
1. To DFMEA
a) Between the characteristics identified during the DFMEA & PFMEA
b) Potential design cause of failure & potential process failure mode
2. To control plan
a) Requirements in PFMEA = Product characteristics
b) Cause of failure mode in PFMEA = Process characteristics
c) Current controls in PFMEA = control methods
Appendix-A – Sample forms
Appendix-B – System level FMEA
Focus on functions & relationships that are unique to the system as a whole (i.e., do not exist at lower levels).
System, sub-system, component level, interfaces, interactions, relationships (lower to higher & higher to lower) are explained through examples
Appendix-C – Alternative risk assessments
Arithmetic combinations of SOD, SO, SD explained
Appendix-D – Alternative analyses techniques
FMECA (criticality)
DRBFM (design review based on failure modes)
FTA (fault tree analysis)